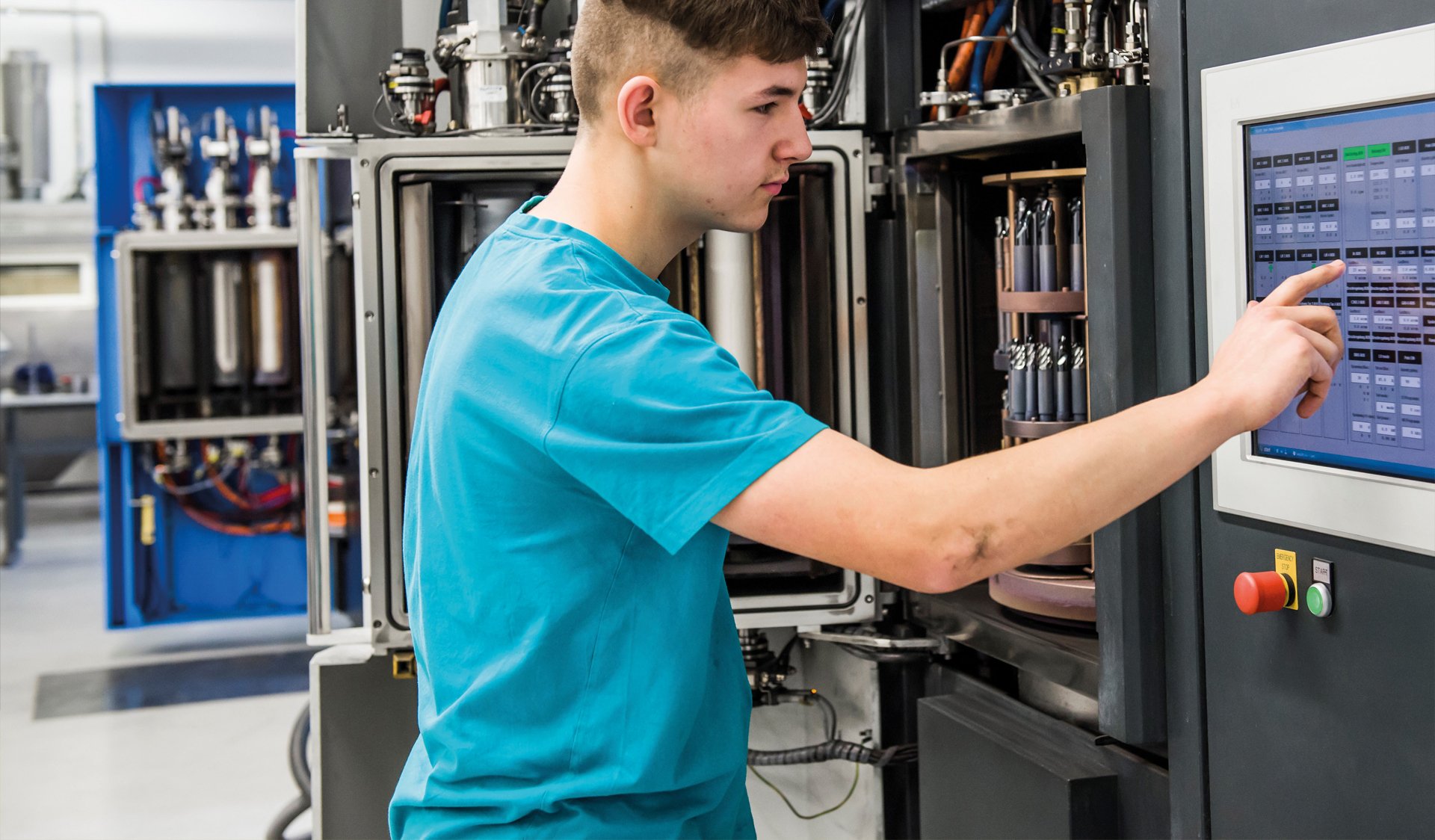
Industrie 4.0
Transferierbare KI in der Zerspanung
Am Projekt mit dem Titel „Beherrschung von Zerspanprozessen durch transferierbare künstliche Intelligenz – Grundlage für Prozessverbesserungen und neue Geschäftsmodelle“ sind insgesamt sieben Partner aus Industrie und Forschung beteiligt. Das vom Bundesministerium für Bildung und Forschung geförderte Forschungsprojekt, das die Möglichkeiten des Transfer Learnings in der Zerspanung ausloten und industriell nutzbar machen soll, läuft seit 2021. Mithilfe von Transfer Learning soll Wissen von bereits gelernten Aufgaben genutzt werden, um ML-Modelle schneller für neue, aber verwandte Aufgaben trainieren zu können.
Die K.-H. Müller Präzisionswerkzeuge GmbH, Robert Bosch GmbH, Botek Präzisionsbohrtechnik GmbH, Empolis Information Management GmbH, Paul Horn GmbH sowie der Lehrstuhl für Fertigungstechnik und Betriebsorganisation FBK der RPTU in Kaiserslautern und das Institut für Werkzeugmaschinen IfW der Universität Stuttgart arbeiten gemeinsam daran, maschinelles Lernen (ML) zur Entscheidungsunterstützung für den Werkzeugwechsel in der Zerspanung effizienter nutzbar zu machen.
Wie bei allen industriellen Anwendungen herrscht auch bei der Zerspanung stetig wachsender Kostendruck. Maßgeblich für die Produktionskosten eines zerspanten Bauteils sind der Werkzeugverschleiß und das Zeitspanvolumen. Durch optimierten Werkzeugeinsatz sollen die Produktionskosten eines zerspanten Bauteils reduziert werden. Nach zwei Jahren Forschungsarbeit zeichnen sich positive Ergebnisse ab.
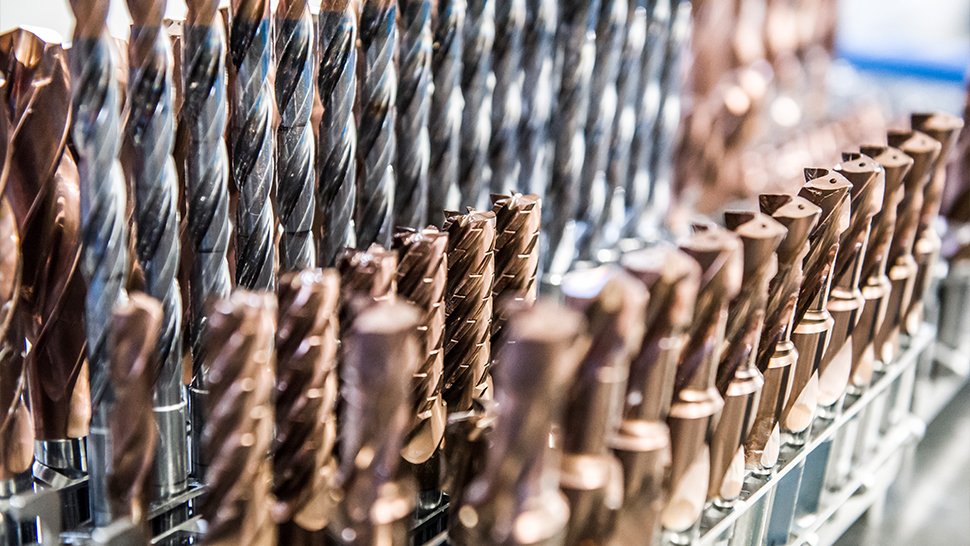
Das Forschungsprojekt soll das Transfer Learning zur Bereitstellung von Modellen des maschinellen Lernens ermöglichen. Die Modelle sollen mit geringem Aufwand auf neue Anwendungsfelder übertragbar sein. Fotos: Müller
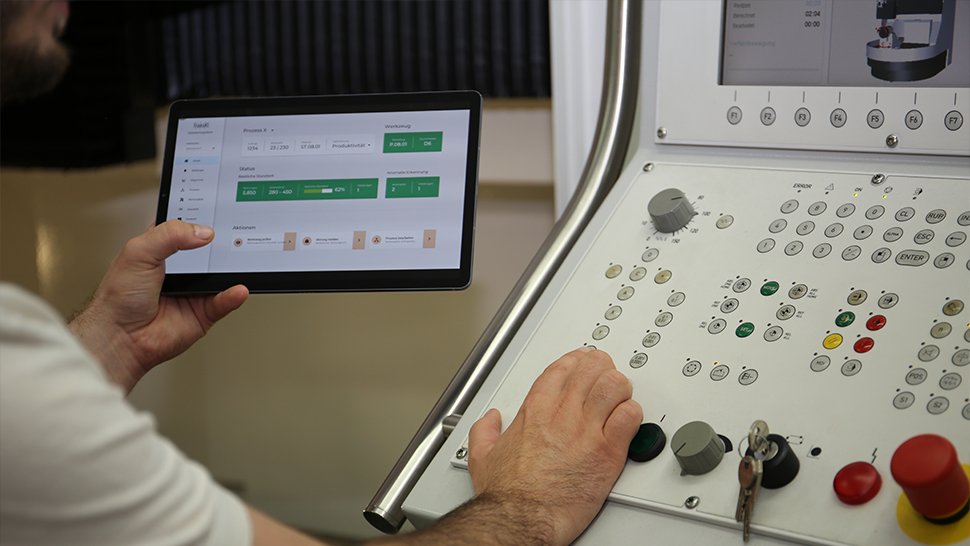
Modelle des maschinellen Lernens werden zur Verschleißprognose von Bohr- und Fräswerkzeugen trainiert. Die Daten kommen direkt aus der Steuerung oder werden von nachrüstbarer Sensorik erhoben.
Aus der Industrie, für die Industrie
Ziel des Projekts ist die Erschließung des Transfer Learnings zur Bereitstellung von Modellen des maschinellen Lernens, die mit geringem Aufwand auf neue Anwendungsfelder übertragbar sind. Dabei werden ML-Modelle zur Verschleißprognose von Bohr- und Fräswerkzeugen auf Daten trainiert, die direkt aus der Steuerung kommen oder mit (leicht) nachrüstbarer Sensorik erhoben werden.
Die Entwicklung der ML-Modelle sowie der Assistenzsysteme erfolgt maßgeblich durch den Projektpartner Empolis Information Management GmbH. Zwei grundlegende Ansätze werden verfolgt.
Zum einen stehen Modelle zur Vorhersage des Remaining Useful Life, kurz RUL, im Fokus. Dabei soll mithilfe von in verschiedenen Anwendungen gesammelten Daten anhand des Verschleißes verlässlich vorhergesagt werden, wie lange ein Werkzeug noch eingesetzt werden kann, bevor es ausgetauscht werden muss.
Zum anderen kommen Modelle zur Anomaliedetektion zum Einsatz. Diese können im Prozess erkennen, ob eine Anomalie auftrat, die beispielsweise durch Spanklemmer oder Ausbrüche am Werkzeug verursacht wurde, und sie können zum anderen auch für die Erkennung des Standzeitendes genutzt werden. Die benötigten Daten werden durch die beteiligten Unternehmen im laufenden Betrieb gesammelt, um das Projekt möglichst nah an der industriellen Realität zu halten.
Dies ist deshalb wichtig, da nicht jede Zerspanung gleich ist. Neben einer Vielzahl an Werkstoffen, die zerspant werden, gilt es auch immer, den Prozess an sich zu beachten. Selbst bei Standardwerkzeugen gibt es signifikante Unterschiede.
Die Werkzeuge bestehen nicht nur aus verschiedenen Materialien – passend zur jeweiligen Anwendung, sondern weisen auch meist unterschiedliche Geometrien und Beschichtungen auf. Die Ergebnisse einer Anwendung lassen sich also nicht problemlos auf andere Anwendungen übertragen.
Darüber hinaus ist das Trainieren der Systeme meist sehr aufwendig. Bislang verfügbare Lösungen zur Optimierung mittels ML beziehen sich in der Regel auf einen spezifischen, meist unter Laborbedingungen betrachteten Zerspanprozess an einem Werkstoff mit definierten Werkzeugen und einem ebenfalls definierten Schnittparameterbereich. Dadurch ist eine Übertragbarkeit der Modelle auf reale, veränderliche Zerspanprozesse in produzierenden Unternehmen mit aktuell gängigen Methoden nicht realisierbar. Dies soll sich nun ändern.
Grundlegende Modelle
In der ersten Phase des Forschungsprojekts wurden industrielle Anwendungsfälle definiert und Zerspanversuche durchgeführt und ausgewertet. Mit den aufbereiteten Daten dieser Versuche wurden grundlegende ML-Modelle entwickelt.
Erste Ergebnisse lassen auf eine gute Leistungsfähigkeit der Modelle auf den steuerungsinternen Daten schließen. Das sind Daten, die Rückschlüsse auf den Prozess zulassen wie Spindel- oder Achsströme. Die erste Phase ist damit erfolgreich abgeschlossen. Diese ist für den Erfolg des Projekts entscheidend, da alle weiteren Schritte auf der hier gewonnen Datenbasis aufbauen.
Im nächsten Schritt wird nun erforscht, wie robust diese Modelle sich gegenüber Variationen bei Prozessparametern, Werkzeugen und Werkstoffen erweisen und wie sie sich möglichst gut auf die variierten Anwendungsfälle übertragen lassen. Dabei wird die Versuchsumgebung, also der Prozess, die Maschine und Sensorik sowie der Werkstoff, schrittweise verändert, verschleißabhängige Gemeinsamkeiten werden identifiziert und Expertenwissen in die Untersuchungen einbezogen.
Um die optimierten ML-Modelle industriell nutzbar zu machen, werden die Modelle in der dritten Projektphase in ein Assistenzsystem integriert, das den Maschinenbediener durch Handlungsempfehlungen für den Werkzeugwechsel unterstützt. Aus den Ausgaben der Modelle können auch Empfehlungen für eine bedarfsgerechte Anpassung des Prozesses abgeleitet werden. Anschließend werden Geschäftsmodelle für die beteiligten Industrieunternehmen entwickelt, die durch den Einsatz der transferierbaren Modelle möglich werden.
Starke Ergebnisse
Für dieses zukunftsweisende und umfängliche Projekt werden Expertise und Ressourcen aus verschiedenen Bereichen benötigt. Deshalb sind insgesamt sieben Partner an der praktischen Umsetzung beteiligt. Die Experten für Präzisionswerkzeuge der K.-H. Müller Präzisionswerkzeuge GmbH koordinieren das Projekt und sind für die Entwicklung innovativer, KI-basierter Geschäftsmodelle zuständig.
Die Robert Bosch GmbH untersucht die Transferierbarkeit der ML-Modelle auf industriell relevante Fräsprozesse und bringt bereits vorhandene Erfahrung im Einsatz von KI-/ML-Methoden in der Produktionstechnik in das Projekt ein. Die Botek Präzisionsbohrtechnik GmbH ist als Industriepartner im Bereich Präzisionsbohrtechnik ein essenzieller Bestandteil des Projekts sowohl bei der Versuchsdurchführung als auch bei der Validierung des Transfer Learnings.
Für die Datenaufbereitung sowie die Entwicklung der ML-Modelle, die Sicherstellung der Transferierbarkeit und die Entwicklung des Assistenzsystems zeichnet die Empolis Information Management GmbH verantwortlich. Die Untersuchung der Zerspanmechanismen beim Bohren und Fräsen mittels parametrischer Modelle und maschinellem Lernen wird am Lehrstuhl für Fertigungstechnik und Betriebsorganisation FBK der TU Kaiserslautern durchgeführt.
Die Hartmetallwerkzeugfabrik Paul Horn GmbH verantwortet die Versuchsdurchführung und -auswertung beim Fräsen und wirkt maßgeblich bei der Datenaufbereitung mit. Das Institut für Werkzeugmaschinen IfW der Universität Stuttgart fokussiert sich auf die Erforschung einer Prozessvorsteuerung und verantwortet die Arbeiten an der Schnittstelle zwischen ML-Modellen und Maschinensteuerung.
Die Projektlaufzeit ist bis 30. Juni 2024 angelegt. Ein Resultat zeigt sich bereits nach der ersten Projektphase: Die sehr gute interdisziplinäre Zusammenarbeit zwischen den Zerspanungsexperten (Müller, Bosch, Botek, Paul Horn, IfW, FBK) und den ML-Experten (Empolis) mündet in einen reibungslosen und wertvollen Wissenstransfer zwischen den beiden Disziplinen.
Kontakt
Mathias Schmidt
Geschäftsführer
K.-H. Müller Präzisionswerkzeuge GmbH
Sien
Tel. +49 6788 9798-0
E-Mail senden