Zerspanwerkzeuge hochproduktiv herstellen!
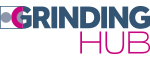

Die Umfangsschneiden von Bohrern, Fräsern und anderen rotationssymmetrischen Zerspanwerkzeugen werden üblicherweise durch eine Aneinanderreihung unterschiedlicher Schleifprozesse hergestellt. Dabei kommen für die Erzeugung der unterschiedlichen Flächen am Schneidkeil mehrere Schleifwerkzeuge zum Einsatz, die nacheinander zunächst die Spanfläche und dann die Freiflächen des Zerspanwerkzeugs bearbeiten. Die einzelnen Schneiden des Zerspanwerkzeugs werden ebenfalls aufeinanderfolgend geschliffen, sodass aufgrund der häufigen Leerbewegungen der Werkzeugmaschine und der erforderlichen Schleifwerkzeugwechsel hohe Nebenzeiten resultieren.
Am Institut für Fertigungstechnik und Werkzeugmaschinen (IFW) der Leibniz Universität Hannover wurde daher ein neues Werkzeugschleifverfahren entwickelt, das diese Herausforderungen adressiert und gleichzeitig die Produktivität bei der Werkzeugfertigung erhöht. Dabei kommt ein kontinuierlicher Wälzschleifprozess zum Einsatz, der die Simultanbearbeitung sämtlicher Umfangsschneiden des Zerspanwerkzeugs ermöglicht und dabei in einem einzigen Prozessschritt mit nur einem Schleifwerkzeug sämtliche Span- und Freiflächen erzeugt. Die hierbei zugrundeliegende Prozesskinematik basiert auf dem kontinuierlichen Wälzschleifen von Zahnrädern, das aufgrund seiner hohen Produktivität bereits seit Jahrzehnten für die Hartfeinbearbeitung von Zahnrädern etabliert ist (Abbildung 1). Neben der hohen Prozessproduktivität war für diese Entwicklung insbesondere dessen verbesserte Fertigungsgüte gegenüber konkurrierenden Verfahren wie dem diskontinuierlichen Profilschleifen ausschlaggebend, die sich in einer verbesserten Rundlauf- und Teilungsgenauigkeit der hergestellten Bauteile äußert.
(s. Abbildung 1: Prozesskinematik beim kontinuierlichen Wälzschleifen von Zahnrädern)
Das klassische Wälzschleifverfahren war jedoch lange Zeit nicht für die Herstellung der stark asymmetrischen und hinterschnittenen Zahnform von Schneidkeilen geeignet und konnte daher bis vor kurzem ausschließlich für die Bearbeitung von Zahnrädern genutzt werden. Um anstelle der Evolvente des Zahnradzahns den asymmetrischen Schneidzahn mit scharfer Schneidkante eines Zerspanwerkzeugs zu erzeugen, mussten deshalb gezielte Prozessmodifikationen vorgenommen werden. So wurden beispielsweise die Geometrie des Schleifwerkzeugs (Schleifschnecke) und die Prozessstellgrößen derart beeinflusst, dass auch der für Fräser und Bohrer charakteristische Hinterschnitt am Schneidkeil erzeugt werden kann.
Die Weiterentwicklung des Verfahrens umfasste im ersten Schritt die Simulation des Schleifprozesses, sodass grundlegende Zusammenhänge zwischen den Prozessstellgrößen, der Schneckengeometrie und der Zielgeometrie des Zerspanwerkzeugs erschlossen werden konnten. Darauf aufbauend ist es dem IFW gelungen, eine Auslegungsmethodik zur gezielten Einstellung der Geometrie des Schneidkeils herzuleiten. Diese Methodik ermöglicht es, innerhalb weniger Iterationsschritte passende Prozessparameter und Schneckengeometrien zur Herstellung einer geforderten Schneidkeilgeometrie des Zerspanwerkzeugs zu bestimmen. Im Anschluss an diese theoretischen Prozessbetrachtungen wurde eine allgemeingültige Herleitung der für den Prozess notwendigen Achskopplungen durchgeführt. Dies ist notwendig, um das Verfahren nicht nur auf Wälzschleifmaschinen, sondern auch auf konventionellen zur Werkzeugherstellung genutzten Maschinen einsetzbar zu machen (Abbildung 2). Zur Verifikation dieser Achskopplungen wurde ein zylindrischer Schleifkörper mit der in der Simulation ermittelte Schneckengeometrie profiliert und anschließend zum Schleifen von Fräsern aus Schnellarbeitsstahl eingesetzt.
(s. Abbildung 2: Kontinuierlicher Wälzschleifprozess zur Herstellung von Zerspanwerkzeugen)
Neben dem Nachweis der praktischen Nutzbarkeit des Verfahrens auf marktüblichen Maschinen konnte so die Qualität der geschliffenen Zerspanwerkzeuge untersucht werden. Dabei wurde festgestellt, dass die geometrische Güte und Schneidkantenqualität der erzeugten Fräswerkzeuge trotz des sehr frühen Entwicklungsstadiums des Wälzschleifverfahrens bereits auf dem Niveau von konventionell geschliffenen Fräswerkzeugen liegen. Außerdem wurde durch die Durchführung einer Kurzstudie gezeigt, dass bei der Herstellung von Fräswerkzeugen zum Stand der Technik vergleichbare Prozesszeiten erzielt werden können. Dabei wurde das sehr hohe Optimierungspotential in Bezug auf das neue Schleifverfahren noch nicht voll ausgeschöpft. Beispielsweise wurde im Gegensatz zum sehr gut erforschten konventionellen Werkzeugschleifprozess bisher weder eine Optimierung der Prozessstellgrößen, noch der Kühlschmierstoffzufuhr oder der Schleifwerkzeugspezifikation vorgenommen. Hinzu kommen prozessspezifische Produktivitätsvorteile, die bei dem neuen Wälzschleifverfahren aus dem Einsatz von mehrgängigen Schleifschnecken oder Shiftbewegungen resultieren und somit beim konventionellen Werkzeugschleifen technologisch nicht einsetzbar sind. Die Shiftbewegung (Abbildung 1) ermöglicht es, dass während des Schleifens kontinuierlich neue Abschnitte der Schleifschnecke in den Eingriff gelangen. Hierdurch kann der auftretende Verschleiß am Schleifwerkzeug direkt kompensiert und somit die hohe Fertigungsgüte des Verfahrens auch in der Großserienfertigung fortlaufend sichergestellt werden. Die ideale Nutzung dieses Potentials wird jedoch ebenso wie der Einsatz von mehrgängigen Schnecken, der zu einer Vervielfachung der Prozessproduktivität führen kann, derzeit noch am IFW erforscht.
In abschließenden Umfangsfräsversuchen wurde zudem die Leistungsfähigkeit der wälzgeschliffenen Fräswerkzeuge ermittelt und den Standzeiten von industriell mit dem konventionellen Verfahren hergestellten Fräsern gegenübergestellt. Bei diesen Untersuchungen wurde festgestellt, dass die Standzeit der Fräswerkzeuge durch die Herstellung mittels kontinuierlichem Wälzschleifen um bis zu 15 % erhöht werden kann. Die Substitution des konventionellen Werkzeugschleifprozesses durch den neu entwickelten Wälzschleifprozess stellt somit ein immenses wirtschaftliches und wissenschaftliches Potential dar, das zukünftig weiter gehoben werden kann. Neben der Erschließung der oben bereits genannten Potentiale wird zukünftig beispielsweise auch die Möglichkeit zur Herstellung ungleichgeteilter Zerspanwerkzeuge durch kontinuierliches Wälzschleifen untersucht, damit anschließend sämtliche industrierelevanten Fräswerkzeuge durch das neue Verfahren hergestellt werden können. Außerdem lassen sich die erarbeiteten Erkenntnisse auf die Herstellung weiterer rotationssymmetrischer Zerspanwerkzeuge übertragen, die neben den eingangs genannten Bohrern und Fräsern unter anderem auch Sägeblätter, Scheibenfräser und Reibahlen umfassen. Die wirtschaftlichen und technologischen Vorteile des neuen Wälzschleifprozesses können somit auf eine Vielzahl weiterer Anwendungsgebiete übertragen werden.
Die Autoren bedanken sich bei der Deutschen Forschungsgemeinschaft (DFG) für die finanzielle Förderung des Forschungsprojektes „Kontinuierliches Wälzschleifen schneidender Verzahnungen 2“ (Fördernummer DE 447/153-2).
Autoren: Dr.-Ing. Mirko Theuer, Prof. Dr.-Ing. Berend Denkena, Herr Dr.-Ing. Alexander Krödel-Worbes
Quelle: Kontinuierliches Wälzschleifen von Zerspanwerkzeugen, Disseration, Mirko Theuer IFW 02/2020, 29.04.2020 (ISBN 978-95900-441-1)