Wir steuern Zukunft
Knochen-Knorpelimplantate aus Biomaterialien
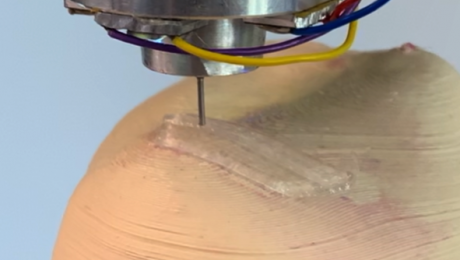
Es sind diese ausführlichen Analysedaten, die die additive Fertigung von personalisierten Produkten ermöglichen. Ein weiteres Projekt im Leistungszentrum Mass Personalization beschäftigt sich mit der additiven Fertigung von personalisierten Knorpelimplantaten. Fehlstellungen, Übergewicht oder Leistungssport können Kniearthrose verursachen. Die Patientin oder der Patient hat Schmerzen und ist in der Bewegungsfreiheit eingeschränkt. Ziel des Projekts ist es, eine durchgängige automatisierte Prozesskette vom CTScan zum personalisierten Implantat zu entwickeln, ermöglicht durch eine umfassende Prozessoptimierung.
Frederik Wulle vom Institut für Steuerungstechnik der Werkzeugmaschinen und Fertigungseinrichtungen (ISW) der Universität Stuttgart betreut das Projekt gemeinsam mit seinen Kolleginnen und Kollegen. Sie erforschen, wie individualisierbare biologische Knochen-Knorpelimplantate aus Biomaterialien automatisiert hergestellt werden können. Wulle ist für die additive Fertigung der Implantate mittels 3D-Druckverfahren zuständig.
„Wir generieren auf Basis der biomechanischen Daten und auf Grundlage der Geometrierekonstruktion die zu druckende Geometrie.“ Die benötigten Daten stammen von den Kolleginnen und Kollegen des IPA. Dort erhalten die Forschenden mithilfe der Analyse daten des Bewegungsapparates Auskunft über Parameter wie Größe und Steifigkeit, die die personalisierten Knorpelimplantate besitzen müssen, um mit der individuellen Biologie und Biomechanik der Person optimal übereinzustimmen und eine erfolgreiche Therapieentwicklung zu ermöglichen.
Mithilfe der Daten rekonstruieren Wulle und seine Kolleginnen und Kollegen die Sollgeometrie der zu ersetzenden Fehlstelle mit computergestützter Konstruktion. Additive Fertigungsverfahren erlauben es, Objekte mit entsprechend komplexer Geometrie aus unterschiedlichen Materialien aufzubauen. Für die Fertigung der Knorpelimplantate setzen sie auf den innovativen mehrachsigen 3D-Druck. Der Vorteil der mehrachsigen Bearbeitung im Vergleich zum herkömmlichen dreiachsigen Verfahren sind die größeren Prozessfreiheiten. So kann beispielsweise der Stufeneffekt minimiert werden, der auftritt, wenn eine Kontur eines Bauteils nicht parallel oder orthogonal zur Aufbaurichtung verläuft und damit die Schräge in einzelne diskrete Schichten untergliedert wird.
Die im Projekt verwendeten Knochen-Knorpelimplantate bestehen aus Biomaterialien. Das interdisziplinäre Forschungsfeld des Bioprintings verfolgt das Ziel, biomimetische Gewebestrukturen als Ersatz für erkranktes Patientengewebe herzustellen. Dabei orientieren sich die Forschenden an biologischem Gewebe und versuchen, dieses in digitalen Druckverfahren nachzubilden. Die Entwicklung, Herstellung und Überprüfung dieser Biomaterialien erfolgt am Institut für Grenzflächenverfahrenstechnik und Plasmatechnologie (IGVP) sowie am Fraunhofer Institut für Grenzflächen und Bioverfahrenstechnik (IGB) in Stuttgart. „Wir hatten die Technologie des mehrachsigen 3D-Drucks entwickelt und suchten eine Anwendung. Unsere Kolleginnen und Kollegen von der Materialentwicklung haben das Potenzial für ihre Anwendung erkannt“, sagt Wulle zu dieser interdisziplinären Zusammenarbeit.
Lesen Sie den gesamten Artikel in: Magazin forschung leben, Ausgabe September 2021, S.52-57
Text: Bettina Künzler
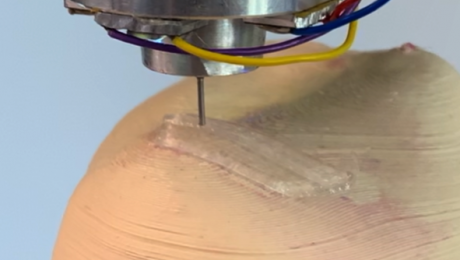
Es sind diese ausführlichen Analysedaten, die die additive Fertigung von personalisierten Produkten ermöglichen. Ein weiteres Projekt im Leistungszentrum Mass Personalization beschäftigt sich mit der additiven Fertigung von personalisierten Knorpelimplantaten. Fehlstellungen, Übergewicht oder Leistungssport können Kniearthrose verursachen. Die Patientin oder der Patient hat Schmerzen und ist in der Bewegungsfreiheit eingeschränkt. Ziel des Projekts ist es, eine durchgängige automatisierte Prozesskette vom CTScan zum personalisierten Implantat zu entwickeln, ermöglicht durch eine umfassende Prozessoptimierung.
Frederik Wulle vom Institut für Steuerungstechnik der Werkzeugmaschinen und Fertigungseinrichtungen (ISW) der Universität Stuttgart betreut das Projekt gemeinsam mit seinen Kolleginnen und Kollegen. Sie erforschen, wie individualisierbare biologische Knochen-Knorpelimplantate aus Biomaterialien automatisiert hergestellt werden können. Wulle ist für die additive Fertigung der Implantate mittels 3D-Druckverfahren zuständig.
„Wir generieren auf Basis der biomechanischen Daten und auf Grundlage der Geometrierekonstruktion die zu druckende Geometrie.“ Die benötigten Daten stammen von den Kolleginnen und Kollegen des IPA. Dort erhalten die Forschenden mithilfe der Analyse daten des Bewegungsapparates Auskunft über Parameter wie Größe und Steifigkeit, die die personalisierten Knorpelimplantate besitzen müssen, um mit der individuellen Biologie und Biomechanik der Person optimal übereinzustimmen und eine erfolgreiche Therapieentwicklung zu ermöglichen.
Mithilfe der Daten rekonstruieren Wulle und seine Kolleginnen und Kollegen die Sollgeometrie der zu ersetzenden Fehlstelle mit computergestützter Konstruktion. Additive Fertigungsverfahren erlauben es, Objekte mit entsprechend komplexer Geometrie aus unterschiedlichen Materialien aufzubauen. Für die Fertigung der Knorpelimplantate setzen sie auf den innovativen mehrachsigen 3D-Druck. Der Vorteil der mehrachsigen Bearbeitung im Vergleich zum herkömmlichen dreiachsigen Verfahren sind die größeren Prozessfreiheiten. So kann beispielsweise der Stufeneffekt minimiert werden, der auftritt, wenn eine Kontur eines Bauteils nicht parallel oder orthogonal zur Aufbaurichtung verläuft und damit die Schräge in einzelne diskrete Schichten untergliedert wird.
Die im Projekt verwendeten Knochen-Knorpelimplantate bestehen aus Biomaterialien. Das interdisziplinäre Forschungsfeld des Bioprintings verfolgt das Ziel, biomimetische Gewebestrukturen als Ersatz für erkranktes Patientengewebe herzustellen. Dabei orientieren sich die Forschenden an biologischem Gewebe und versuchen, dieses in digitalen Druckverfahren nachzubilden. Die Entwicklung, Herstellung und Überprüfung dieser Biomaterialien erfolgt am Institut für Grenzflächenverfahrenstechnik und Plasmatechnologie (IGVP) sowie am Fraunhofer Institut für Grenzflächen und Bioverfahrenstechnik (IGB) in Stuttgart. „Wir hatten die Technologie des mehrachsigen 3D-Drucks entwickelt und suchten eine Anwendung. Unsere Kolleginnen und Kollegen von der Materialentwicklung haben das Potenzial für ihre Anwendung erkannt“, sagt Wulle zu dieser interdisziplinären Zusammenarbeit.
Lesen Sie den gesamten Artikel in: Magazin forschung leben, Ausgabe September 2021, S.52-57
Text: Bettina Künzler
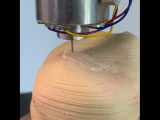