Wir steuern Zukunft
Smarte Kabelmontage
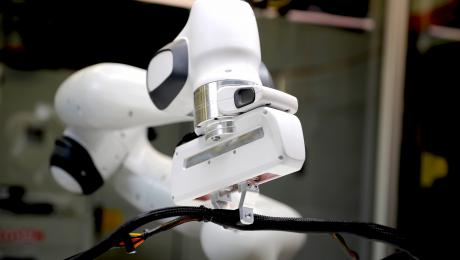
Der Blick in die Rohkarosserie des Fahrzeugs zeigt eine ungeordnete Ansammlung meterlanger Kabel. Markus Wnuk, Wissenschaftler am Institut für Steuerungstechnik der Werkzeugmaschinen und Fertigungseinrichtungen der Universität Stuttgart (ISW) beschreibt es so: "Wir sehen hier eine sehr unstrukturierte Szene. Das ist ein schlechtes Ausgangsszenario für die Automatisierung." Deswegen werden auch im Zeitalter von Industrie 4.0 Leitungssätze, auch Kabelbäume genannt, nach wie vor vollständig von Hand im Fahrzeug ausgelegt und angebracht - vom Auspacken der Kabelbaumtasche bis zur letzten Befestigung. "Was die Automatisierung schwierig macht, ist die enorme Variantenvielfalt, denn kein Leitungssatz wird zweimal gefertigt", sagt der Experte.
Das liegt an der enormen Anzahl an Bauteilen und Montageoperationen, den sehr kleinen Kontaktsystemen, aber vor allem auch am Material. Kabel sind biegeschlaff und leicht deformierbar. Sie verdrehen sich, bilden Schlaufen und verändern ihre Form praktisch bei jeder Berührung. Um Komponenten wie diese dennoch automatisiert montieren zu können, entwickeln die Wissenschaftlerinnen und Wissenschaftler des ISW in Kooperation mit Forschen den des Exzellenzclusters SimTech neue Methoden, mit denen verfügbare Sensordaten und neue Simulationstechnologien kombiniert werden können. Ziel ist es, die Echtzeitsimulation einer Maschine direkt in deren Steuerungssystem zu integrieren und so Produktionsprozesse im laufenden Betrieb zu optimieren.
DEN BEDARF IM BLICK BEHALTEN
Ihre Forschung stößt in der Industrie auf fruchtbaren Boden. Denn einen mobilen Roboter so zu programmieren, dass er auch komplexe Fertigungsprozesse autonom durchführen kann, ist eine Herausforderung. Insbesondere, da sich die Produktionsumgebungen immer dynamischer verändern und die Produkte sich zunehmend individualisieren. "Der Leidensdruck ist hoch", beobachtet der Institutsleiter des ISW, Prof. Alexander Verl. An der Spitze des aus dem Cluster heraus entstandenen Industriekonsortiums „IC SimTech" setzt sich Verl für den Transfer von neuem Know-how in die Industrie und für einen engen Austausch mit den potenziellen Anwendern ein. Die datenintegrierte Simulationswissenschaft boome, berichtet er. Die Evaluierung, Automatisierung, Optimierung und Visualisierung von Fertigungsprozessen auf der Basis der Daten, die die Maschinen selbst produzieren, stehen in der Forschungsförderung und der Industrie ganz oben auf der Agenda.
Umso wichtiger ist es, nicht am Bedarf vorbei zu entwickeln. Als Bindeglied zwischen Grundlagenforschung und Anwendung will das "IC SimTech" nicht nur über die neuen Methoden und Modelle informieren, sondern auch deren Implementierung in die industrielle Praxis aktiv vorantreiben. So organisiert das Konsortium unter anderem bilaterale Projekte mit regionalen, nationalen und internationalen Industriepartnern. Es unterstützt Promovenden und Postdocs bei der Zusammenarbeit mit Industriepartnern oder ermutigt sie, ihre Ideen in Start-ups einzubringen.
AUSTAUSCH ÜBER AKTUELLE FORSCHUNGSTHEMEN
"Wir wollen die Unternehmen über unsere Forschungsthemen auf dem Laufenden halten. Aber wir brauchen auch ihr Feedback, um zu prüfen, ob unsere wissenschaftlichen Annahmen realistisch sind", erläutert Wnuk. Im Rahmen des 2020 gestarteten und von der Deutschen Forschungsgemeinschaft (DFG) geförderten Projektes „DataCon" arbeitet der Ingenieur gerade an einem weiteren wichtigen Baustein für den Transfer: Ein Demonstrator, dessen erster Use Case konkret die Montage von Kabelbäumen adressiert, soll die Potenziale datenintegrierter Simulationen aufzeigen und die Sichtbarkeit von SimTech in den produzierenden Branchen weiter erhöhen. Angesprochen werden damit interessierte Unternehmen vor allem in der Automobilindustrie.
Das Produktionsmodell soll veranschaulichen, wie die im Prozess laufend aktualisierten Simulationsdaten mit den Messdaten der Maschine fusioniert werden können, um einen Industrieroboter für die Kabelmontage möglichst präzise zu steuern. Bei der Entwicklung der entsprechenden Steuerungssoftware arbeiten sich die SimTech-Expertinnen und -Experten im Austausch mit ihren Praxispartnern von Teilproblem zu Teilproblem vor. Im ersten Schritt soll der Roboter lernen, ein deformierbares Objekt wie ein Kabel mittels der zusammengeführten Daten richtig zu lokalisieren. Das bedeutet vor allem, den jeweiligen Griffpunkt zu erkennen und schließlich das Objekt in die richtige Endlage zu positionieren. 2023 soll der Demonstrator fertig sein und unter anderem auf Messen zum Einsatz kommen.
"Wir wollen, dass unsere Entwicklungen für die Industrie nützlich sind", betont Verl. Bis das neue Montagesystem "von der Stange" gefertigt werden kann, ist es zwar noch ein weiter Weg. Aber für den Leiter des ISW liegt der Wert von transferorientierten Forschungsprojekten ohnehin nicht nur im verkaufsfähigen Endprodukt. Ihm geht es auch um die Lernerfahrungen seiner Studierenden, von denen der allergrößte Teil später in der Industrie arbeitet. "Ich möchte, dass auch etwas in den Köpfen der Menschen hängen bleibt."
Text: Jutta Witte
Quelle: Das Magazin der Universität Stuttgart "forschung leben", Ausgabe März 2021
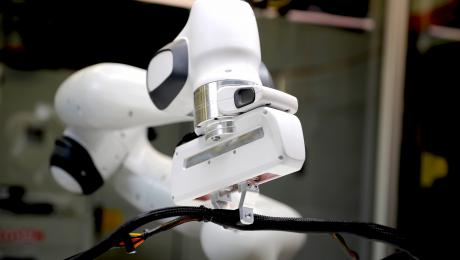
Der Blick in die Rohkarosserie des Fahrzeugs zeigt eine ungeordnete Ansammlung meterlanger Kabel. Markus Wnuk, Wissenschaftler am Institut für Steuerungstechnik der Werkzeugmaschinen und Fertigungseinrichtungen der Universität Stuttgart (ISW) beschreibt es so: "Wir sehen hier eine sehr unstrukturierte Szene. Das ist ein schlechtes Ausgangsszenario für die Automatisierung." Deswegen werden auch im Zeitalter von Industrie 4.0 Leitungssätze, auch Kabelbäume genannt, nach wie vor vollständig von Hand im Fahrzeug ausgelegt und angebracht - vom Auspacken der Kabelbaumtasche bis zur letzten Befestigung. "Was die Automatisierung schwierig macht, ist die enorme Variantenvielfalt, denn kein Leitungssatz wird zweimal gefertigt", sagt der Experte.
Das liegt an der enormen Anzahl an Bauteilen und Montageoperationen, den sehr kleinen Kontaktsystemen, aber vor allem auch am Material. Kabel sind biegeschlaff und leicht deformierbar. Sie verdrehen sich, bilden Schlaufen und verändern ihre Form praktisch bei jeder Berührung. Um Komponenten wie diese dennoch automatisiert montieren zu können, entwickeln die Wissenschaftlerinnen und Wissenschaftler des ISW in Kooperation mit Forschen den des Exzellenzclusters SimTech neue Methoden, mit denen verfügbare Sensordaten und neue Simulationstechnologien kombiniert werden können. Ziel ist es, die Echtzeitsimulation einer Maschine direkt in deren Steuerungssystem zu integrieren und so Produktionsprozesse im laufenden Betrieb zu optimieren.
DEN BEDARF IM BLICK BEHALTEN
Ihre Forschung stößt in der Industrie auf fruchtbaren Boden. Denn einen mobilen Roboter so zu programmieren, dass er auch komplexe Fertigungsprozesse autonom durchführen kann, ist eine Herausforderung. Insbesondere, da sich die Produktionsumgebungen immer dynamischer verändern und die Produkte sich zunehmend individualisieren. "Der Leidensdruck ist hoch", beobachtet der Institutsleiter des ISW, Prof. Alexander Verl. An der Spitze des aus dem Cluster heraus entstandenen Industriekonsortiums „IC SimTech" setzt sich Verl für den Transfer von neuem Know-how in die Industrie und für einen engen Austausch mit den potenziellen Anwendern ein. Die datenintegrierte Simulationswissenschaft boome, berichtet er. Die Evaluierung, Automatisierung, Optimierung und Visualisierung von Fertigungsprozessen auf der Basis der Daten, die die Maschinen selbst produzieren, stehen in der Forschungsförderung und der Industrie ganz oben auf der Agenda.
Umso wichtiger ist es, nicht am Bedarf vorbei zu entwickeln. Als Bindeglied zwischen Grundlagenforschung und Anwendung will das "IC SimTech" nicht nur über die neuen Methoden und Modelle informieren, sondern auch deren Implementierung in die industrielle Praxis aktiv vorantreiben. So organisiert das Konsortium unter anderem bilaterale Projekte mit regionalen, nationalen und internationalen Industriepartnern. Es unterstützt Promovenden und Postdocs bei der Zusammenarbeit mit Industriepartnern oder ermutigt sie, ihre Ideen in Start-ups einzubringen.
AUSTAUSCH ÜBER AKTUELLE FORSCHUNGSTHEMEN
"Wir wollen die Unternehmen über unsere Forschungsthemen auf dem Laufenden halten. Aber wir brauchen auch ihr Feedback, um zu prüfen, ob unsere wissenschaftlichen Annahmen realistisch sind", erläutert Wnuk. Im Rahmen des 2020 gestarteten und von der Deutschen Forschungsgemeinschaft (DFG) geförderten Projektes „DataCon" arbeitet der Ingenieur gerade an einem weiteren wichtigen Baustein für den Transfer: Ein Demonstrator, dessen erster Use Case konkret die Montage von Kabelbäumen adressiert, soll die Potenziale datenintegrierter Simulationen aufzeigen und die Sichtbarkeit von SimTech in den produzierenden Branchen weiter erhöhen. Angesprochen werden damit interessierte Unternehmen vor allem in der Automobilindustrie.
Das Produktionsmodell soll veranschaulichen, wie die im Prozess laufend aktualisierten Simulationsdaten mit den Messdaten der Maschine fusioniert werden können, um einen Industrieroboter für die Kabelmontage möglichst präzise zu steuern. Bei der Entwicklung der entsprechenden Steuerungssoftware arbeiten sich die SimTech-Expertinnen und -Experten im Austausch mit ihren Praxispartnern von Teilproblem zu Teilproblem vor. Im ersten Schritt soll der Roboter lernen, ein deformierbares Objekt wie ein Kabel mittels der zusammengeführten Daten richtig zu lokalisieren. Das bedeutet vor allem, den jeweiligen Griffpunkt zu erkennen und schließlich das Objekt in die richtige Endlage zu positionieren. 2023 soll der Demonstrator fertig sein und unter anderem auf Messen zum Einsatz kommen.
"Wir wollen, dass unsere Entwicklungen für die Industrie nützlich sind", betont Verl. Bis das neue Montagesystem "von der Stange" gefertigt werden kann, ist es zwar noch ein weiter Weg. Aber für den Leiter des ISW liegt der Wert von transferorientierten Forschungsprojekten ohnehin nicht nur im verkaufsfähigen Endprodukt. Ihm geht es auch um die Lernerfahrungen seiner Studierenden, von denen der allergrößte Teil später in der Industrie arbeitet. "Ich möchte, dass auch etwas in den Köpfen der Menschen hängen bleibt."
Text: Jutta Witte
Quelle: Das Magazin der Universität Stuttgart "forschung leben", Ausgabe März 2021

