Get There Faster.
Latetst News by ModuleWorks Digital Manufacturing
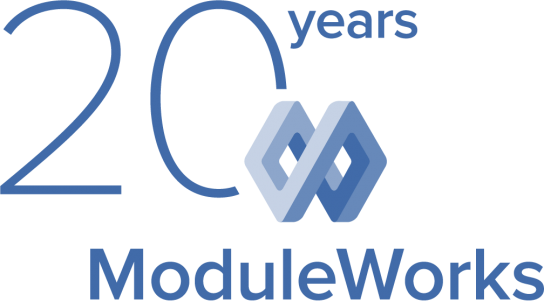
Welcome to the summer edition of the ModuleWorks Digital Manufacturing Newsletter. In this edition, we’re looking forward to seeing you soon at EMO in Hannover. We’d also like to offer a glimpse of our 2023.08 Release which is available now from the Customer Login section of the ModuleWorks website. And don’t forget to check out What's New 2023.08 - YouTube.
Discover how ModuleWorks' automated intelligence opens up new manufacturing possibilities. Click the button below to book your meeting with Julia Meyer-Hendricks or Sebastian Wallraff, our Heads of Digital Manufacturing. We look forward to seeing you soon!
You will find us here:
Hall 009, Booth D08
We invite you to book a meeting here.
What's New in ModuleWorks 2023.08
5-Axis Deburring – Allow Asymmetric Edge Shapes
Deburring normally tries to maintain a constant tool contact point with the deburr edge to ensure symmetrical edge breaks or chamfers. However, in difficult-to-reach areas, the tool needs to tilt away to avoid collisions. To accommodate the need for tilting and greater tool reach, we have introduced a new feature that allows the contact point of the tool to change during deburring. This can alter the shape of the edge, resulting in asymmetric edges. This is why we give operators the choice of whether to allow asymmetric edges as a trade-off between reachability and the accuracy of the shape of the edge break.
Multi-Axis Roughing
With this new feature for Multi-Axis Roughing you can define an additional offset to extend the machining area beyond the 3D containment curve. This enables over-machining in open stock situations and allows the tool to get closer to workpiece geometries, such as the walls of a pocket.
Automatic 3+2 Axis Roughing
Two new features extend our auto 3+2 roughing portfolio. Identify link positions when relinking: Operators need commands on the CNC control for locking the machine axes and ensuring the required rigidity during machining. This is why we have added markers to the toolpath, enabling integrators to trigger. the commands that initiate locking.Clearance blend spline feed rate: Manually set the feed rate for link motions between the indexed orientations.
Multi-Axis Profiling
For multi-axis profiling, you can now define the contact point of the tool with the curve. This provides greater manual control and flexibility over how the tool is used. For example, cutting with the cylindrical part of the flute enables the tool to withstand greater forces, while cutting with the tool tip can offer greater precision.
3-Axis Machining - Report Minimum shaft Length
This feature helps you choose the most appropriate tool for the machining operation. It calculates the minimum shaft length you need to reach all areas of the programmed toolpath without causing a collision.
3-Axis Machining - Cusp Height Control for Corner Pegs
This feature lets you control the maximum cusp height when corner peg motions are necessary. It automatically matches the overall cusp height setting from the standard step over calculation within the pattern. This delivers more constant rest material and optimizes the part for rest roughing as well as finishing.
Turn-Milling
For turn-milling, the machining areas are now cleaned up more efficiently.
- You can now detect the “flat” areas of the rotary part and remove the material at the actual part height.
- Remove rest material on the corners that was left by the Y-axis tool shift.
Both features help to remove more material and avoid extra operations.
Probing
We’ve added a new product to our portfolio: Probing. This first version offers 3D touch point probing. Here’s how it works: Pick any points on a part. The system automatically recognizes the part geometry and uses it to calculate a probing toolpath that delivers collision-free approach and retract motions. The toolpath can be exported as a canned cycle compatible with the native probing cycle on the control.
Simulation - Interpolation turning
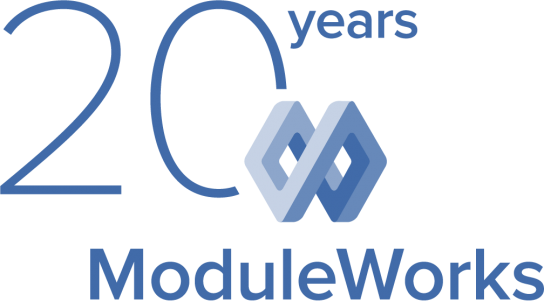
Welcome to the summer edition of the ModuleWorks Digital Manufacturing Newsletter. In this edition, we’re looking forward to seeing you soon at EMO in Hannover. We’d also like to offer a glimpse of our 2023.08 Release which is available now from the Customer Login section of the ModuleWorks website. And don’t forget to check out What's New 2023.08 - YouTube.
Discover how ModuleWorks' automated intelligence opens up new manufacturing possibilities. Click the button below to book your meeting with Julia Meyer-Hendricks or Sebastian Wallraff, our Heads of Digital Manufacturing. We look forward to seeing you soon!
You will find us here:
Hall 009, Booth D08
We invite you to book a meeting here.
What's New in ModuleWorks 2023.08
5-Axis Deburring – Allow Asymmetric Edge Shapes
Deburring normally tries to maintain a constant tool contact point with the deburr edge to ensure symmetrical edge breaks or chamfers. However, in difficult-to-reach areas, the tool needs to tilt away to avoid collisions. To accommodate the need for tilting and greater tool reach, we have introduced a new feature that allows the contact point of the tool to change during deburring. This can alter the shape of the edge, resulting in asymmetric edges. This is why we give operators the choice of whether to allow asymmetric edges as a trade-off between reachability and the accuracy of the shape of the edge break.
Multi-Axis Roughing
With this new feature for Multi-Axis Roughing you can define an additional offset to extend the machining area beyond the 3D containment curve. This enables over-machining in open stock situations and allows the tool to get closer to workpiece geometries, such as the walls of a pocket.
Automatic 3+2 Axis Roughing
Two new features extend our auto 3+2 roughing portfolio. Identify link positions when relinking: Operators need commands on the CNC control for locking the machine axes and ensuring the required rigidity during machining. This is why we have added markers to the toolpath, enabling integrators to trigger. the commands that initiate locking.Clearance blend spline feed rate: Manually set the feed rate for link motions between the indexed orientations.
Multi-Axis Profiling
For multi-axis profiling, you can now define the contact point of the tool with the curve. This provides greater manual control and flexibility over how the tool is used. For example, cutting with the cylindrical part of the flute enables the tool to withstand greater forces, while cutting with the tool tip can offer greater precision.
3-Axis Machining - Report Minimum shaft Length
This feature helps you choose the most appropriate tool for the machining operation. It calculates the minimum shaft length you need to reach all areas of the programmed toolpath without causing a collision.
3-Axis Machining - Cusp Height Control for Corner Pegs
This feature lets you control the maximum cusp height when corner peg motions are necessary. It automatically matches the overall cusp height setting from the standard step over calculation within the pattern. This delivers more constant rest material and optimizes the part for rest roughing as well as finishing.
Turn-Milling
For turn-milling, the machining areas are now cleaned up more efficiently.
- You can now detect the “flat” areas of the rotary part and remove the material at the actual part height.
- Remove rest material on the corners that was left by the Y-axis tool shift.
Both features help to remove more material and avoid extra operations.
Probing
We’ve added a new product to our portfolio: Probing. This first version offers 3D touch point probing. Here’s how it works: Pick any points on a part. The system automatically recognizes the part geometry and uses it to calculate a probing toolpath that delivers collision-free approach and retract motions. The toolpath can be exported as a canned cycle compatible with the native probing cycle on the control.
Simulation - Interpolation turning
