Get There Faster.
News: ModuleWorks Weaving Pattern with Automatic Amplitude Adjustment
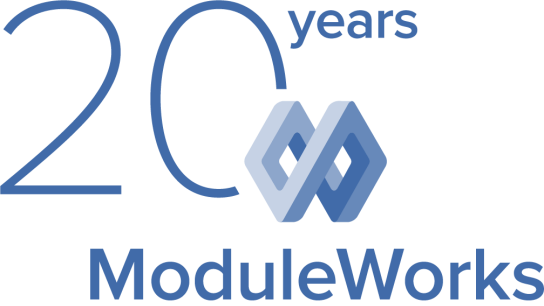
Additive and Process Technologies
ModuleWorks has a unique approach to supporting different additive technologies and combining them in a software library. While considering the requirements of each technology and process, ModuleWorks transfers the latest developments from one technology to another. This ensures continuous technological enhancements for solving individual customer challenges.
The powerful ModuleWorks toolpath and simulation software library provides full flexibility for fast and seamless integration into manufacturing technology infrastructures. The libraries support a wide range of additive technologies, such as Powder Bed Fusion, DED, Polymer Printing or Wire-Arc Additive Manufacturing.
The latest advances in the ModuleWorks wire-arc technology support weaving with automatic amplitude adjustment:
Weaving with Automatic Amplitude
for Varying Wall Widths
Weaving patterns are an indispensable part of any additive manufacturing portfolio, bolstering the strength of parts and adding aesthetic appeal to products. The latest ModuleWorks weaving toolpath further automates weaving workflows by intelligently adjusting the amplitude of the pattern as the width of the wall varies. This eliminates the need for manual adjustments, speeds up deposition and ensures consistent, high quality build-up along the entire wall.
Optimized point distribution on the weaving track generates uninterrupted feed motions and the toolpath calculation applies automatic collision avoidance to the weaving pattern for safe, efficient manufacturing of freeform and non-freeform geometries on machine tools and robots.
ModuleWorks Weaving Toolpath:
- Highly automated manufacturing of parts with varying thickness and wall structures.
- Apply multiple weaving patterns on top of each other.
- Apply weaving on freeform surfaces.
- Alternate the start direction and the order in which the toolpaths are generated for each layer. This avoids over-deposition at a single start point and prevents accumulation of heat flow in a single direction to reduce residual stresses during deposition.
- Adjust the start and end margins to prevent overlapping and over-deposition at intersections.
- Zig Zag function to minimize the number of nozzle retracts.
- Adjust the weave parameters such as thickness and step size for individual containment regions for more precise printing
Meet ModuleWorks at EMO 2023
Sustainable production is center stage at EMO 2023. The ModuleWorks Additive & Process Technologies Team is there to discuss your challenges with you. Discover how ModuleWorks' automated intelligence opens up new additive possibilities. We look forward to seeing you soon!
You will find us here:
Hall 009, Stand D08
18-23 September 2023
Learn more about the ModuleWorks weaving pattern and how ModuleWorks helps you rapidly enhance the performance and quality of your robotic additive and 3D printing applications.
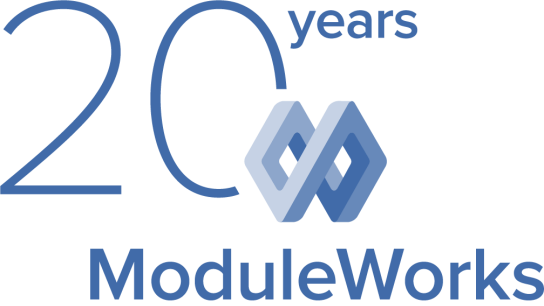
Additive and Process Technologies
ModuleWorks has a unique approach to supporting different additive technologies and combining them in a software library. While considering the requirements of each technology and process, ModuleWorks transfers the latest developments from one technology to another. This ensures continuous technological enhancements for solving individual customer challenges.
The powerful ModuleWorks toolpath and simulation software library provides full flexibility for fast and seamless integration into manufacturing technology infrastructures. The libraries support a wide range of additive technologies, such as Powder Bed Fusion, DED, Polymer Printing or Wire-Arc Additive Manufacturing.
The latest advances in the ModuleWorks wire-arc technology support weaving with automatic amplitude adjustment:
Weaving with Automatic Amplitude
for Varying Wall Widths
Weaving patterns are an indispensable part of any additive manufacturing portfolio, bolstering the strength of parts and adding aesthetic appeal to products. The latest ModuleWorks weaving toolpath further automates weaving workflows by intelligently adjusting the amplitude of the pattern as the width of the wall varies. This eliminates the need for manual adjustments, speeds up deposition and ensures consistent, high quality build-up along the entire wall.
Optimized point distribution on the weaving track generates uninterrupted feed motions and the toolpath calculation applies automatic collision avoidance to the weaving pattern for safe, efficient manufacturing of freeform and non-freeform geometries on machine tools and robots.
ModuleWorks Weaving Toolpath:
- Highly automated manufacturing of parts with varying thickness and wall structures.
- Apply multiple weaving patterns on top of each other.
- Apply weaving on freeform surfaces.
- Alternate the start direction and the order in which the toolpaths are generated for each layer. This avoids over-deposition at a single start point and prevents accumulation of heat flow in a single direction to reduce residual stresses during deposition.
- Adjust the start and end margins to prevent overlapping and over-deposition at intersections.
- Zig Zag function to minimize the number of nozzle retracts.
- Adjust the weave parameters such as thickness and step size for individual containment regions for more precise printing
Meet ModuleWorks at EMO 2023
Sustainable production is center stage at EMO 2023. The ModuleWorks Additive & Process Technologies Team is there to discuss your challenges with you. Discover how ModuleWorks' automated intelligence opens up new additive possibilities. We look forward to seeing you soon!
You will find us here:
Hall 009, Stand D08
18-23 September 2023
Learn more about the ModuleWorks weaving pattern and how ModuleWorks helps you rapidly enhance the performance and quality of your robotic additive and 3D printing applications.
