Smart Manufacturing Solutions
Bearbeitungszentren erfüllen enge Toleranzvorgaben bei der Schwenklager-Herstellung für Porsche
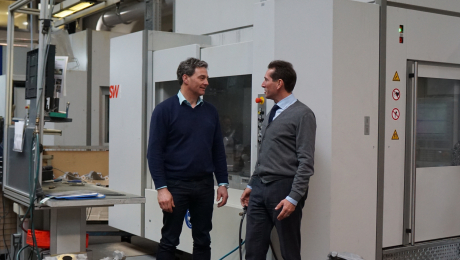
Anlagenzuverlässigkeit führt zur Steigerung der Fertigungsqualität sowie Integration eines stabilen Fertigungsprozesses für die nächsten fünf Jahre
Seit 2013 fertigt die Schabmüller Automobiltechnik GmbH die Schwenklager des Porsche Macan. Die Zerspanung erfolgt mithilfe der hochpräzisen Bearbeitungszentren (BAZ) BA W06-22 und BA one6 der Schwäbische Werkzeugmaschinen GmbH (SW), die speziell für anspruchsvolle Aufgaben in der Serienfertigung ausgelegt sind. Die hohe Präzision der Maschinen ist gerade in der Automobilbranche essentiell, da der hohe Qualitätsanspruch nur geringe Toleranzen gestattet. Während die zweispindlige BA W06-22 für die Hauptlagerbohrung, die Federbein- und Querlenkeranbindung eingesetzt wird, erfolgt die Bremssattelanbindung in einem zweiten Schritt auf der einspindligen BA one6. Allein bei letzterem konnte eine wesentliche Qualitätssteigerung in den Fertigungsprozess integriert und verwirklicht werden.
Dass die Bearbeitung der wöchentlich 1.700 Satz Schwenklager, die bei Schabmüller für Porsche gefertigt werden, auf zwei unterschiedlichen Maschinentypen stattfindet, war eine bewusste, strategische Entscheidung des Großmehringer Automobilzulieferers: Mit der Fertigung der Hauptlagerbohrungen, der Schwanenhalsanbindung (Federbeinstütze) und der Querlenker erfolgen 90 Prozent der Bearbeitung innerhalb der vom Endkunden Porsche geforderten Taktzeit in einem Halbkugel-Zugriff von oben auf der zweispindligen BA W06-22. Die Größe des Bauteils sowie die zu produzierende Jahresstückzahl bestimmen die Anzahl der Spindeln. Da die Zerspanung der Bremssattelanbindung aufgrund der Werkstückspannung in der OP 10 nicht realisiert werden kann und der Bearbeitungsanteil sehr viel geringer ist, erfolgt dieser Bearbeitungsschritt auf der einspindligen BA one6. „So können parallel die Bearbeitungsschritte der OP 10 und OP 20 durchgeführt werden“, erklärt Helmut Häckl, technischer Leiter bei Schabmüller. Darüber hinaus kann die BA one6 im Bedarfsfall auch zur Kompensation von Produktionsspitzen verwendet werden.
Um den strengen Kriterien des Automobilzulieferers – unter anderem dürfen die Positionstoleranzen in jeder Achse teilweise nur zwei bis drei Hundertstel betragen – gerecht zu werden, sind die SW-Maschinen dabei exakt auf diese Anwendungsfelder abgestimmt. So sind Fehler nahezu ausgeschlossen, da ein pneumatisches Auflage-Kontrollsystem prüft, ob das Bauteil richtig in der Vorrichtung gespannt ist – andernfalls wird der Prozess nicht gestartet. Abweichungen können dadurch sofort registriert und behoben werden. Zudem erhöht die Werkzeug-Plananlagenkontrolle die Prozesssicherheit, indem das Werkzeug an der HSK-Schnittstelle der Spindel geprüft wird. Durch Linearantriebstechnik in allen Achsen, die im Gegensatz zum Kugelgewindeantrieb einen äußerst geringen Verschleiß aufweisen, konnte zudem die vom Endkunden geforderte Taktzeit verwirklicht und eine dauerhaft gleichbleibende Werkstückqualität erreicht werden. Auch fällt die Wärmeausdehnung der Direktantriebe bedeutend geringer aus als bei konventionellen Antrieben, so dass eine hohe Langzeitgenauigkeit zugesagt werden kann. Zusätzlich werden die Maschinen inhouse bei Schabmüller alle drei bis fünf Jahre teil- beziehungsweise generalüberholt, um die hochgenaue Fertigung auch langfristig zu garantieren.
Eines der schnellsten Bearbeitungszentren: BA W06-22
Die verwendete BA W06-22 mit einem Spindelabstand von 600 mm zeichnet sich unter anderem durch ihre minimalen Span-zu-Span-Zeiten von 2,75 s aus, die eine hochgenaue Zerspanung von Leichtmetallwerkstücken in kürzester Zeit ermöglichen. Vor allem benötigt sie nur 0,7 s Hochlaufzeit von 0 auf 17.500 Umdrehungen und erreicht Hauptantriebsachsbeschleunigungswerte von bis zu 2 G, was sie zu einem der schnellsten BAZ macht, die aktuell auf dem Markt zu finden sind. Der Arbeitsraum pro Spindel beträgt 600 x 600 x 500 mm.
Zudem ist die Maschine in Monoblockbauweise konzipiert, was die Durchbiegung minimiert und einen optimalen Kraftfluss zwischen der Bearbeitungseinheit und dem Werkstückträger gewährleistet, sowie mit einer Box-in-Box 3-Achseinheit, die speziell für hochdynamische Zerspanoperationen im Leichtmetallsektor entwickelt wurde. Diese 3-Achseinheit ist als Stahl-Schweißkonstruktion ausgeführt, sodass die bewegten Massen bei höchster Systemsteifigkeit gering gehalten werden. „Sie wird rückseitig in den Monoblock eingesetzt, die horizontale Anordnung der Arbeitsspindeln ermöglicht dabei einen freien Fall der Späne“, erläutert Matthias Maier, Vertriebsleiter bei SW. Ein Doppelschwenkträger mit integrierten Rundachsen (Torque) ermöglicht darüber hinaus ein hauptzeitparalleles Be- und Entladen. Zusätzlich sind die SW-Maschinen so ausgelegt, dass sie sich ideal für das Be- und Entladen mit einem Roboter, auch von oben über ein Portal, eignen.
BA one6 liefert Positionstoleranzen von < 0,005 mm
Die einspindlige BA one6, die wie die BA W06-22 auf die Bearbeitung von Werkstücken aus nicht-magnetischen Werkstoffen wie Aluminium- oder Titanlegierungen ausgelegt ist, bietet einen Arbeitsraum von 600 x 650 x 500 mm. „Der Fokus dieses Modelltyps liegt auf der Zerspanung mit höchsten Genauigkeitsanforderungen“, so Maier. Linear- und Torquemotoren in den Vorschubachsen garantieren auch hier höchste Werkstückgenauigkeit mit einer Positionstoleranz von weniger als 0,005 mm bei maximaler Dynamik und sehr kurzen Nebenzeiten. Die Span-zu-Span-Zeit beträgt lediglich 2,5 s.
Ausgerüstet ist die BA one6 ebenfalls mit einem Doppelschwenkträger für das hauptzeitparallele Be- und Entladen von Werkstücken. Da der Aufbau der Maschine identisch mit dem der BA W06-22 ist, eignet sie sich bestens für gemeinsame Verkettungen: Sie dient als passende Ergänzung mehrspindliger Fertigungslinien für die einspindlige Vor- oder Nachbearbeitung großer Leichtmetallwerkstücke, aber auch zum Ausgleich von Produktionsspitzen, wenn beispielsweise ein Zweispindler nicht ausreicht und ein drei- oder vierspindliges BAZ aufgrund der Bauteilgröße nicht eingesetzt werden kann.
Erwartete Einsparungen durch Erhöhung der Qualität und Integration einer prozesssicheren Fertigung
Insgesamt erzielt Schabmüller durch den Einsatz der SW-Maschinen eine hohe Bearbeitungsqualität und einen reproduzierbaren Fertigungsprozess. Dies wirkt sich erheblich auf die Ressource Personal in den Bereichen Qualitätssicherung und Instandhaltung aus. Zudem verringert sich durch die Optimierung der Schnittdaten die Bearbeitungszeit in der BA one6. Um einem Stillstand der Maschinen vorzubeugen, bietet SW mit den sogenannten PULSE-Dienstleistungen zudem Fernwartung sowie -diagnose oder eine vorbeugende Wartung an, bei der sich ein Spezialist in die jeweilige Maschine einschaltet und den Kunden über notwendige Schritte informiert. „Generell geht es immer darum, einem Stillstand der Maschinen vorzubeugen – denn das kann für den Kunden weitreichende Folgen haben und hohe Kosten verursachen“, fasst Maier zusammen. Zwischen Schabmüller und SW finden hierzu regelmäßig Service-Workshops statt. Die dabei anfallenden Optimierungsvorschläge werden anschließend von Seiten des Maschinenherstellers auch entwicklungstechnisch umgesetzt. „Wir gehen besonders auf die Probleme und Anforderungen unserer Kunden ein und entwickeln auch speziell für die Anwender“, erklärt Maier die Arbeit von SW. So wird Technologie immer wieder individuell erarbeitet.
„Für die Maschinen von SW haben wir uns entschieden, weil die hohe Qualität für die nötige Ruhe im Projekt sorgt“, berichtet Häckl. „So können wir nicht nur Zeit, sondern auch Geld einsparen. Zudem arbeiten wir bereits seit 1994 mit SW zusammen, sodass gegenseitiges Vertrauen vorherrscht und die notwendige Technik bereits im Haus ist.“ Ein wichtiger Faktor ist auch die mit diesen Maschinen zu erwartende reibungslose Fertigung innerhalb der Projektlaufzeiten von viereinhalb bis fünf Jahren. „Über diesen Zeitraum gesehen können so erhebliche Kosten eingespart werden, die wir mit Sicherheit in dieser Zeitspanne in Reparaturen oder ähnliches hätten investieren müssen, wenn wir ‚billig’ eingekauft hätten“, schätzt Häckl.
Schabmüller hat derzeit insgesamt 21 SW-Maschinen im Einsatz. Davon sind etliche durch die seit 2015 zu SW gehörende bartsch GmbH automatisiert im Einsatz. Bis 2019 wird in Großmehring eine zweite Halle sukzessive mit SW-Maschinen bestückt, in der dann noch einmal 17 automatisierte Bearbeitungszentren eingesetzt werden. Darin sollen jährlich bis zu 680.000 Zylinderkopfhauben für den Endkunden Audi hergestellt werden.
Franz Schabmüller, der ursprünglich Hoflader für Ställe mit engen Gassen baute, gründete am 1. Januar 1978 die Schabmüller Maschinenbau GmbH in Holzkirchen, die heute als Schabmüller Automobiltechnik GmbH Großserienfertiger und Partner von beispielsweise Audi, Porsche, Volkswagen oder BMW tätig ist. Kernkompetenz des Unternehmens sind Leistungen in den Bereichen Großserie, Fräs- und Drehtechnik, Montage sowie Dichtprüfungen, wobei Schabmüller besonders auf die Fräsbearbeitung von Aluminiumkokillengussteilen spezialisiert ist. Das Teilespektrum des Unternehmens umfasst unter anderem Lagerrahmen, Zylinderkopfhauben, Kurbelwellenlagerdeckel, Steuergehäuse, Ölwannen sowie die Schwenklager und Radträger für den Porsche Macan. In 80 Prozent der Fälle tritt Schabmüller als Tier 2 auf, in den restlichen Fällen als Tier 1. Das Unternehmen gehört zusammen mit den Firmen MONTES GmbH & Co. KG, ZBG Zerspanungstechnik Bruck GmbH, ZMT Automotive GmbH & Co. KG, WELCO GmbH & Co. KG, FS Technologies GmbH & Co. KG sowie MONTES Hungária Kft. zur Schabmüller-Gruppe. Aktuell sind bei der Schabmüller Automobiltechnik GmbH etwa 140 Mitarbeiter in den Unternehmensbereichen Zerspanung und Montage tätig, davon 14 Prozent Auszubildende.
Die Schwäbische Werkzeugmaschinen GmbH (SW) mit Sitz in Schramberg-Waldmössingen ist ein international agierender Lösungslieferant für anspruchsvolle, werkstückspezifische Fertigungssysteme zur Metallbearbeitung. Eine Kernkompetenz sind dabei mehrspindlige Hochleistungsbearbeitungszentren, von denen inzwischen weltweit mehr als 2.000 bei Kunden unterschiedlichster Branchen installiert wurden. Darüber hinaus entwickelt das Unternehmen im eigenen Technologiezentrum auch stetig neue Zerspanungsmöglichkeiten oder optimiert bestehende Techniken, um für jede Anwendung die passende Lösung bieten zu können. Hinzu kommt ein umfassendes Portfolio an Service- und Beratungsleistungen. Aktuell beschäftigt SW rund 590 Mitarbeiter und konnte 2015 einen Umsatz von 280 Mio. Euro verzeichnen.
Kontakt
Schabmüller Automobiltechnik GmbH
Dieselstraße 10, 85098 Großmehring
InTerPark Ingolstadt
Tel.: 08456 9677-0, Fax: 08456 9677-50
E-Mail: info@schabmueller.com
Internet: www.schabmueller.com
Schwäbische Werkzeugmaschinen GmbH
Seedorfer Strasse 91, 78713 Schramberg-Waldmössingen
Tel.: 07402 74-0, Fax: 07402 74-211
E-Mail: contact@sw-machines.de
Internet: www.sw-machines.de
Mehr Info für die Redaktion
ABOPR Pressedienst B.V., Büro München
Leonrodstraße 68, 80636 München
Tel.: 089 500315-20, Fax: 089 500315-15
E-Mail: info@abopr.de
Internet: www.abopr.de
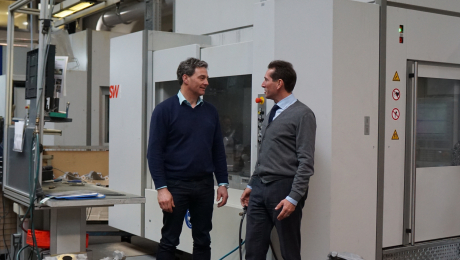
Anlagenzuverlässigkeit führt zur Steigerung der Fertigungsqualität sowie Integration eines stabilen Fertigungsprozesses für die nächsten fünf Jahre
Seit 2013 fertigt die Schabmüller Automobiltechnik GmbH die Schwenklager des Porsche Macan. Die Zerspanung erfolgt mithilfe der hochpräzisen Bearbeitungszentren (BAZ) BA W06-22 und BA one6 der Schwäbische Werkzeugmaschinen GmbH (SW), die speziell für anspruchsvolle Aufgaben in der Serienfertigung ausgelegt sind. Die hohe Präzision der Maschinen ist gerade in der Automobilbranche essentiell, da der hohe Qualitätsanspruch nur geringe Toleranzen gestattet. Während die zweispindlige BA W06-22 für die Hauptlagerbohrung, die Federbein- und Querlenkeranbindung eingesetzt wird, erfolgt die Bremssattelanbindung in einem zweiten Schritt auf der einspindligen BA one6. Allein bei letzterem konnte eine wesentliche Qualitätssteigerung in den Fertigungsprozess integriert und verwirklicht werden.
Dass die Bearbeitung der wöchentlich 1.700 Satz Schwenklager, die bei Schabmüller für Porsche gefertigt werden, auf zwei unterschiedlichen Maschinentypen stattfindet, war eine bewusste, strategische Entscheidung des Großmehringer Automobilzulieferers: Mit der Fertigung der Hauptlagerbohrungen, der Schwanenhalsanbindung (Federbeinstütze) und der Querlenker erfolgen 90 Prozent der Bearbeitung innerhalb der vom Endkunden Porsche geforderten Taktzeit in einem Halbkugel-Zugriff von oben auf der zweispindligen BA W06-22. Die Größe des Bauteils sowie die zu produzierende Jahresstückzahl bestimmen die Anzahl der Spindeln. Da die Zerspanung der Bremssattelanbindung aufgrund der Werkstückspannung in der OP 10 nicht realisiert werden kann und der Bearbeitungsanteil sehr viel geringer ist, erfolgt dieser Bearbeitungsschritt auf der einspindligen BA one6. „So können parallel die Bearbeitungsschritte der OP 10 und OP 20 durchgeführt werden“, erklärt Helmut Häckl, technischer Leiter bei Schabmüller. Darüber hinaus kann die BA one6 im Bedarfsfall auch zur Kompensation von Produktionsspitzen verwendet werden.
Um den strengen Kriterien des Automobilzulieferers – unter anderem dürfen die Positionstoleranzen in jeder Achse teilweise nur zwei bis drei Hundertstel betragen – gerecht zu werden, sind die SW-Maschinen dabei exakt auf diese Anwendungsfelder abgestimmt. So sind Fehler nahezu ausgeschlossen, da ein pneumatisches Auflage-Kontrollsystem prüft, ob das Bauteil richtig in der Vorrichtung gespannt ist – andernfalls wird der Prozess nicht gestartet. Abweichungen können dadurch sofort registriert und behoben werden. Zudem erhöht die Werkzeug-Plananlagenkontrolle die Prozesssicherheit, indem das Werkzeug an der HSK-Schnittstelle der Spindel geprüft wird. Durch Linearantriebstechnik in allen Achsen, die im Gegensatz zum Kugelgewindeantrieb einen äußerst geringen Verschleiß aufweisen, konnte zudem die vom Endkunden geforderte Taktzeit verwirklicht und eine dauerhaft gleichbleibende Werkstückqualität erreicht werden. Auch fällt die Wärmeausdehnung der Direktantriebe bedeutend geringer aus als bei konventionellen Antrieben, so dass eine hohe Langzeitgenauigkeit zugesagt werden kann. Zusätzlich werden die Maschinen inhouse bei Schabmüller alle drei bis fünf Jahre teil- beziehungsweise generalüberholt, um die hochgenaue Fertigung auch langfristig zu garantieren.
Eines der schnellsten Bearbeitungszentren: BA W06-22
Die verwendete BA W06-22 mit einem Spindelabstand von 600 mm zeichnet sich unter anderem durch ihre minimalen Span-zu-Span-Zeiten von 2,75 s aus, die eine hochgenaue Zerspanung von Leichtmetallwerkstücken in kürzester Zeit ermöglichen. Vor allem benötigt sie nur 0,7 s Hochlaufzeit von 0 auf 17.500 Umdrehungen und erreicht Hauptantriebsachsbeschleunigungswerte von bis zu 2 G, was sie zu einem der schnellsten BAZ macht, die aktuell auf dem Markt zu finden sind. Der Arbeitsraum pro Spindel beträgt 600 x 600 x 500 mm.
Zudem ist die Maschine in Monoblockbauweise konzipiert, was die Durchbiegung minimiert und einen optimalen Kraftfluss zwischen der Bearbeitungseinheit und dem Werkstückträger gewährleistet, sowie mit einer Box-in-Box 3-Achseinheit, die speziell für hochdynamische Zerspanoperationen im Leichtmetallsektor entwickelt wurde. Diese 3-Achseinheit ist als Stahl-Schweißkonstruktion ausgeführt, sodass die bewegten Massen bei höchster Systemsteifigkeit gering gehalten werden. „Sie wird rückseitig in den Monoblock eingesetzt, die horizontale Anordnung der Arbeitsspindeln ermöglicht dabei einen freien Fall der Späne“, erläutert Matthias Maier, Vertriebsleiter bei SW. Ein Doppelschwenkträger mit integrierten Rundachsen (Torque) ermöglicht darüber hinaus ein hauptzeitparalleles Be- und Entladen. Zusätzlich sind die SW-Maschinen so ausgelegt, dass sie sich ideal für das Be- und Entladen mit einem Roboter, auch von oben über ein Portal, eignen.
BA one6 liefert Positionstoleranzen von < 0,005 mm
Die einspindlige BA one6, die wie die BA W06-22 auf die Bearbeitung von Werkstücken aus nicht-magnetischen Werkstoffen wie Aluminium- oder Titanlegierungen ausgelegt ist, bietet einen Arbeitsraum von 600 x 650 x 500 mm. „Der Fokus dieses Modelltyps liegt auf der Zerspanung mit höchsten Genauigkeitsanforderungen“, so Maier. Linear- und Torquemotoren in den Vorschubachsen garantieren auch hier höchste Werkstückgenauigkeit mit einer Positionstoleranz von weniger als 0,005 mm bei maximaler Dynamik und sehr kurzen Nebenzeiten. Die Span-zu-Span-Zeit beträgt lediglich 2,5 s.
Ausgerüstet ist die BA one6 ebenfalls mit einem Doppelschwenkträger für das hauptzeitparallele Be- und Entladen von Werkstücken. Da der Aufbau der Maschine identisch mit dem der BA W06-22 ist, eignet sie sich bestens für gemeinsame Verkettungen: Sie dient als passende Ergänzung mehrspindliger Fertigungslinien für die einspindlige Vor- oder Nachbearbeitung großer Leichtmetallwerkstücke, aber auch zum Ausgleich von Produktionsspitzen, wenn beispielsweise ein Zweispindler nicht ausreicht und ein drei- oder vierspindliges BAZ aufgrund der Bauteilgröße nicht eingesetzt werden kann.
Erwartete Einsparungen durch Erhöhung der Qualität und Integration einer prozesssicheren Fertigung
Insgesamt erzielt Schabmüller durch den Einsatz der SW-Maschinen eine hohe Bearbeitungsqualität und einen reproduzierbaren Fertigungsprozess. Dies wirkt sich erheblich auf die Ressource Personal in den Bereichen Qualitätssicherung und Instandhaltung aus. Zudem verringert sich durch die Optimierung der Schnittdaten die Bearbeitungszeit in der BA one6. Um einem Stillstand der Maschinen vorzubeugen, bietet SW mit den sogenannten PULSE-Dienstleistungen zudem Fernwartung sowie -diagnose oder eine vorbeugende Wartung an, bei der sich ein Spezialist in die jeweilige Maschine einschaltet und den Kunden über notwendige Schritte informiert. „Generell geht es immer darum, einem Stillstand der Maschinen vorzubeugen – denn das kann für den Kunden weitreichende Folgen haben und hohe Kosten verursachen“, fasst Maier zusammen. Zwischen Schabmüller und SW finden hierzu regelmäßig Service-Workshops statt. Die dabei anfallenden Optimierungsvorschläge werden anschließend von Seiten des Maschinenherstellers auch entwicklungstechnisch umgesetzt. „Wir gehen besonders auf die Probleme und Anforderungen unserer Kunden ein und entwickeln auch speziell für die Anwender“, erklärt Maier die Arbeit von SW. So wird Technologie immer wieder individuell erarbeitet.
„Für die Maschinen von SW haben wir uns entschieden, weil die hohe Qualität für die nötige Ruhe im Projekt sorgt“, berichtet Häckl. „So können wir nicht nur Zeit, sondern auch Geld einsparen. Zudem arbeiten wir bereits seit 1994 mit SW zusammen, sodass gegenseitiges Vertrauen vorherrscht und die notwendige Technik bereits im Haus ist.“ Ein wichtiger Faktor ist auch die mit diesen Maschinen zu erwartende reibungslose Fertigung innerhalb der Projektlaufzeiten von viereinhalb bis fünf Jahren. „Über diesen Zeitraum gesehen können so erhebliche Kosten eingespart werden, die wir mit Sicherheit in dieser Zeitspanne in Reparaturen oder ähnliches hätten investieren müssen, wenn wir ‚billig’ eingekauft hätten“, schätzt Häckl.
Schabmüller hat derzeit insgesamt 21 SW-Maschinen im Einsatz. Davon sind etliche durch die seit 2015 zu SW gehörende bartsch GmbH automatisiert im Einsatz. Bis 2019 wird in Großmehring eine zweite Halle sukzessive mit SW-Maschinen bestückt, in der dann noch einmal 17 automatisierte Bearbeitungszentren eingesetzt werden. Darin sollen jährlich bis zu 680.000 Zylinderkopfhauben für den Endkunden Audi hergestellt werden.
Franz Schabmüller, der ursprünglich Hoflader für Ställe mit engen Gassen baute, gründete am 1. Januar 1978 die Schabmüller Maschinenbau GmbH in Holzkirchen, die heute als Schabmüller Automobiltechnik GmbH Großserienfertiger und Partner von beispielsweise Audi, Porsche, Volkswagen oder BMW tätig ist. Kernkompetenz des Unternehmens sind Leistungen in den Bereichen Großserie, Fräs- und Drehtechnik, Montage sowie Dichtprüfungen, wobei Schabmüller besonders auf die Fräsbearbeitung von Aluminiumkokillengussteilen spezialisiert ist. Das Teilespektrum des Unternehmens umfasst unter anderem Lagerrahmen, Zylinderkopfhauben, Kurbelwellenlagerdeckel, Steuergehäuse, Ölwannen sowie die Schwenklager und Radträger für den Porsche Macan. In 80 Prozent der Fälle tritt Schabmüller als Tier 2 auf, in den restlichen Fällen als Tier 1. Das Unternehmen gehört zusammen mit den Firmen MONTES GmbH & Co. KG, ZBG Zerspanungstechnik Bruck GmbH, ZMT Automotive GmbH & Co. KG, WELCO GmbH & Co. KG, FS Technologies GmbH & Co. KG sowie MONTES Hungária Kft. zur Schabmüller-Gruppe. Aktuell sind bei der Schabmüller Automobiltechnik GmbH etwa 140 Mitarbeiter in den Unternehmensbereichen Zerspanung und Montage tätig, davon 14 Prozent Auszubildende.
Die Schwäbische Werkzeugmaschinen GmbH (SW) mit Sitz in Schramberg-Waldmössingen ist ein international agierender Lösungslieferant für anspruchsvolle, werkstückspezifische Fertigungssysteme zur Metallbearbeitung. Eine Kernkompetenz sind dabei mehrspindlige Hochleistungsbearbeitungszentren, von denen inzwischen weltweit mehr als 2.000 bei Kunden unterschiedlichster Branchen installiert wurden. Darüber hinaus entwickelt das Unternehmen im eigenen Technologiezentrum auch stetig neue Zerspanungsmöglichkeiten oder optimiert bestehende Techniken, um für jede Anwendung die passende Lösung bieten zu können. Hinzu kommt ein umfassendes Portfolio an Service- und Beratungsleistungen. Aktuell beschäftigt SW rund 590 Mitarbeiter und konnte 2015 einen Umsatz von 280 Mio. Euro verzeichnen.
Kontakt
Schabmüller Automobiltechnik GmbH
Dieselstraße 10, 85098 Großmehring
InTerPark Ingolstadt
Tel.: 08456 9677-0, Fax: 08456 9677-50
E-Mail: info@schabmueller.com
Internet: www.schabmueller.com
Schwäbische Werkzeugmaschinen GmbH
Seedorfer Strasse 91, 78713 Schramberg-Waldmössingen
Tel.: 07402 74-0, Fax: 07402 74-211
E-Mail: contact@sw-machines.de
Internet: www.sw-machines.de
Mehr Info für die Redaktion
ABOPR Pressedienst B.V., Büro München
Leonrodstraße 68, 80636 München
Tel.: 089 500315-20, Fax: 089 500315-15
E-Mail: info@abopr.de
Internet: www.abopr.de
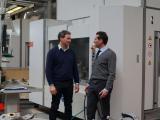
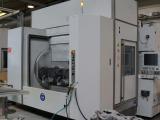
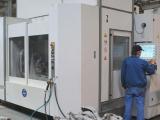


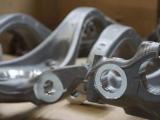

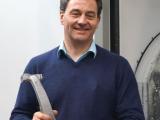
