Mit Tempo glänzen - Hochvorschub-Hartdrehen
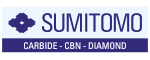
Um beim Hartdrehen gute Oberflächen zu erzeugen wird allgemein mit geringem Vorschub gearbeitet, was in der Regel eine relativ lange Bearbeitungszeit je Werkstück bedeutet. Weil aber immer höhere Produktivität gefordert wird, hat Sumitomo nun das HFT-System für das Hochvorschubdrehen (High Feed Turning) entwickelt, das die Bearbeitungszeiten um den Faktor 6 bis 10 kürzen kann. Bei Schnittgeschwindigkeiten vc bis zu 150 m/min und einer Spantiefe ap von 0,15 mm, als Beispiel für ein Werkstück aus Einsatzstahl mit einer Härte etwa 60 HRC, erscheinen die Werte eher gewöhnlich für das Hartdrehen. Den Unterschied macht dann der vergleichsweise große Vorschub f in Höhe von 1,2 mm pro Umdrehung. Das gibt der Produktivität einen großen Schub. Mit einem nachgeschalteten Schlichtdurchgang unter vermindertem Vorschub ergeben sich nahezu glänzende Oberflächen.
Voraussetzung für das neue Hochvorschubdrehen sind sehr steife Maschinen- und Werkzeugbedingungen. Das heißt, es braucht eine sehr steife und schwingungsdämpfende Maschine, die auch über ausreichend hohe Drehmomente verfügt. Darauf abgestimmt sind auch die sehr steifen Monoblock-Werkzeughalter von Sumitomo, damit diese Steifigkeit auch bis zur Schneide durchgehalten wird. Die ausgeklügelten Plattensitze der Werkzeuge leiten die um den Faktor 2 bis 3 höheren Schneidkräfte optimal und ohne Vibrationen in die Maschine ab. Die Schneiden selbst bestehen aus einer Acht-Kant-Wendeschneidplatte mit einem Voll-CBN-Belag der gesamten Plattenoberfläche. Daher ist die Platte ungewöhnlich robust und kann sowohl in der Trockenbearbeitung als auch unter Emulsion eingesetzt werden, was deren Einsatzbereich sehr universell macht. Auch hier kommt es auf Steifigkeit und besten Spanfluss ebenso an, wie auf die optimale Nutzung des Schneidstoffes CBN. Daher hat man sich für eine Wendeschneidplatte mit acht Schneiden entschieden, was die Zahl der benötigten Wendeschneidplatten und damit die Werkzeugkosten für den Kunden senkt. Die Schneidengeometrie beinhaltet eine sogenannte Wiper-Geometrie, ist also mit einer sogenannten Schleppschneide versehen, die die Oberfläche des Werkstückes nach dem eigentlichen Schnitt glättet. So sind lange Standzeiten, hohe Schnittgeschwindigkeiten und glänzende Oberflächen gewährleistet.
Das Hochvorschub-Drehverfahren ist auf einfachen Standardmaschinen machbar und kann so von vielen Kunden ohne große Investition genutzt werden. Bisher zeigen sich sehr gute Ergebnisse nicht nur in hoch legierten und gehärteten Stählen, sondern auch in schwer zerspanbaren Materialien wie Titanlegierungen oder Inconel.
Das Verfahren funktioniert nicht nur bei der Außenbearbeitung, sondern auch bei Innenbearbeitungen mittlerer und größerer Durchmesser. Ein typisches Beispiel ist die Innenbohrung eines Planetenzahnrades, bei dem es auf die Oberflächengüte und gewünschte Ölrillen ankommt. Der unterbrochene Schnitt aufgrund der Ölbohrungen kann mit den CBN-Platten von Sumitomo gut gemeistert werden. Im Vergleich zum normalen Hartdrehen konnte eine Produktivitätssteigerung um das Sechsfache erreicht werden.
Ein weiteres Beispiel aus der Praxis ist ein Gelenkbolzen mit Fläche und großer Bohrung. Hier ergibt sich ein stark unterbrochener Schnitt, was bei der vorherigen Hartbearbeitung einen hohen Schneidenverbrauch verursacht hat. Pro Schneide konnten bislang nur 3 - 5 Werkstücke bearbeitet werden. Die verwendeten Schneidplatten hatten nur zwei Schneiden, was also hohe Werkzeugkosten und häufige Werkzeugwechsel bedeutete. Mit den neuen Werkzeugen und dem Hoch-Vorschub-Drehverfahren können jetzt 35 - 40 Werkstücke je Schneidkante hergestellt werden. Der Bearbeitungsprozess ist um Faktor 10 schneller, was die Produktivität um 92% dramatisch steigert. Mit den acht Schneidkanten können nun pro Wendeschneidplatte sagenhafte 320 Werkstücke gefertigt werden. Da steht die Wirtschaftlichkeit des Verfahrens außer Frage.