Adaptive Prüfplanung mithilfe eines digitalen Zwillings für die virtuelle Qualitätssicherung
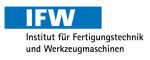

Zur Reduzierung vermeidbarer Prüfaufwände wird im Projekt VerticalE2E ein digitaler Zwilling zur adaptiven Prüfplanung erforscht. Die neuesten Erkenntnisse hierzu wurden im Rahmen der CIRP Conference on Manufacturing Systems vor internationalem Fachpublikum präsentiert. So können durch die Einbindung datenbasierter Qualitätsprognosen in den Prüfplanungsprozess eine aufwandsarme 100%-Prüfung durchgeführt und vermeidbare Prüfaufwände identifiziert werden. Des Weiteren haben die Ergebnisse gezeigt, dass die Hinzunahme von Simulationsdaten sowie die Verwendung von Methoden des maschinellen Lernens gegenüber herkömmlichen Regressionsverfahren zu deutlichen Steigerungen der Prognosegüte führen können.
Die Fertigung von Luftfahrtkomponenten ist geprägt durch umfangreiche Prüfprozesse, um die hohen Qualitätsanforderungen (u.a. durch die EN 9100) sicherzustellen. Die Bauteilprüfung an sich bringt jedoch keine Wertsteigerung für das Werkstück, stattdessen verursacht sie einen hohen Zeit- und Kostenaufwand. Im Projekt VerticalE2E wird daher an einer adaptiven Vorgehensweise zur Reduzierung von vermeidbaren Prüfaufwänden geforscht. Durch die Integration eines digitalen Zwillings in den Prüfplanungsprozess kann das virtuelle Messergebnis als Filter genutzt werden, um vermeidbare Prüfaufwände zu identifizieren und so zu reduzieren. Somit werden lediglich Werkstücke geprüft, die durch den digitalen Zwilling nicht eindeutig in die Kategorien "OK" oder "nicht OK" eingeordnet werden.
Innerhalb der CAD-CAM-Kette erfolgt die Prüfplanung typischerweise parallel zur oder nach der CAM-Planung und findet meist einmalig für ein bestimmtes Produkt statt. Alle Schritte der Qualitätsprüfung (u.a. Prüfmerkmale, -mittel, -umfang) sind damit festgelegt. Eine individuelle Anpassung der notwendigen Prüfungen pro Werkstück wird nicht vorgenommen. Voraussetzung zur virtuellen Prüfung ist das Vorliegen eines digitalen Fußabdrucks des gefertigten Werkstücks. Dieser umfasst sämtliche relevante Fertigungsdaten (Maschinen-, Sensor-, Simulations- und Qualitätsdaten), welche synchronisiert für jedes Werkstück gespeichert sind. Aufgrund variierender Datenformate und Auslesefrequenzen stellt dieser Prozessschritt eine besondere Herausforderung zur Implementierung einer adaptiven Prüfplanung dar.
Darauf aufbauend erfolgt die Modellierung der Werkstückqualität im digitalen Werkstückzwilling innerhalb der Materialabtragsimulation. Durch die Einbindung von virtuellen Prüfmitteln (hier: Regressionsmodelle) wird die erreichte Qualität datenbasiert ermittelt. Das Ergebnis der Qualitätsmodellierung ist schließlich neues Wissen über die vorhandene Werkstückqualität. Anhand des Ergebnisses wird eine virtuelle Entscheidung über die weitere Qualitätsprüfung des Werkstücks getroffen. Im Falle einer eindeutigen Entscheidung, ist keine weitere physische Prüfung notwendig und der Prüfplan wird reduziert. Nur, wenn der ermittelte Qualitätswert nah an der Toleranzgrenze liegt, ist eine physische Prüfung erforderlich. In diesem Fall kann ohne die physische Prüfung nicht mit ausreichender Sicherheit davon ausgegangen werden, dass die virtuelle Qualitätsprüfung eindeutig ist.
Auf der CIRP Conference on Manufacturing Systems in Kapstadt wurden kürzlich aktuelle Ergebnisse aus dem Forschungsprojekt auf internationaler Bühne präsentiert. So wurde für das 3-achsige Taschenfräsen von Aluminiumwerkstücken die Modellgüte zur Prognose der Oberflächenrauheit Ra sowie der Formabweichung ds untersucht. Hierbei konnte festgestellt werden, dass eine Hinzunahme von Simulationsdaten (Zeitspanvolumen Qw und Werkzeugumschlingungswinkel ϕ) zu den Maschinen- und Sensordaten (Vorschubgeschwindigkeit vf und Aktivkraft Fa) den zu erwartenden Modellfehler um bis zu 34 % reduziert. Bei Verwendung der Gaußprozess-Regression liegt ein mittlerer Modellfehler zwischen 7,1 % und 11,1 % vor. Bei Prognosen der Formabweichung ds konnte die Hinzunahme von Simulationsdaten keine Verbesserung der Prognosegenauigkeit bewirken. Allerdings ist eine signifikante Modellverbesserung (+40 %) durch die Verwendung von Methoden des maschinellen Lernens gegenüber herkömmlichen Regressionsverfahren zu erzielen. Ein mittlerer prozentualer Fehler von 8,5 % - 11,5 % ist in diesem Zusammenhang ermittelt worden.
Die Ergebnisse zeigen, dass mithilfe datenbasierter Ansätze bereits hohe Genauigkeiten zur aufwandsarmen Bestimmung der Werkstückqualität erzielt werden können. Die Integration von datenbasierten Entscheidungen in Planungsabläufe besitzt somit ein hohes Potenzial zur Effizienzsteigerung und Reduzierung des notwendigen Erfahrungswissens. „Die Vorstellung und Diskussion der aktuellen Forschungsergebnisse vor dem internationalen Publikum war eine tolle Erfahrung. Zusätzlich konnte ich während der Konferenz noch weitere wertvolle Kontakte knüpfen“, so Projektbearbeiter Leon Reuter.
Für weitere Informationen steht Ihnen Leon Reuter, Institut für Fertigungstechnik und Werkzeugmaschinen der Leibniz Universität Hannover, unter Telefon +49 511 762 18211 oder per E-Mail (reuter@ifw.uni-hanover.de) gern zur Verfügung.