Einblicke in zukünftige Produktionstechnik beim Abschlusssymposium des Zukunftslabors Produktion
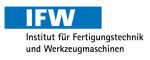

Auf dem Abschlusssymposium des Zukunftslabors Produktion wurden die Ergebnisse von 5 Jahren Forschung zur Digitalisierung in der Druckgusswertschöpfungskette präsentiert. Das betrachtete Spektrum reichte von der Datengewinnung durch das Retrofitting von Bestandsanlagen bis hin zum unternehmensübergreifenden Datenaustausch. In einer Diskussionsrunde mit Industrievertretern konnten aktuelle Chancen und Herausforderungen diskutiert werden. Die Ergebnisse zeigen, dass die Digitalisierung der Produktionsprozesse Effizienz steigert und unternehmensübergreifende Lösungen ermöglicht.
Am 26.09.2024 fand das Abschlusssymposium des Projekts „Zukunftslabor Produktion“ am Produktionstechnischen Zentrum Hannover in Garbsen statt. Fünf Jahre Forschung zur Digitalisierung der Produktion entlang der Druckgusswertschöpfungskette wurden erfolgreich abgeschlossen und vorgestellt. Die besonderen Highlights waren der Impulsvortrag und die Diskussionsrunde. In ersterem gab Dr.-Ing. Marc-André Dittrich von DMG MORI einen Ausblick auf die Situation und Bedarfe von Werkzeugmaschinen in der Wertschöpfungskette und deren digitaler Vernetzung in 2050. Kurz- und Mittelfristige Chancen und Herausforderungen konnten in der Diskussionsrunde mit Dr.-Ing. Agnetha Flore vom Zentrum für digitale Innovationen Niedersachsen, Dr.-Ing. Marc-André Dittrich von DMG MORI und Dr.-Ing. Oliver Maiß von ECOROLL differenziert betrachtet werden.
Die Vision des Zukunftslabors war eine durchgängig digitale Produktionskette, welche im Projekt durch modulare, in sich greifenden Teilprojekten erarbeitet wurde. Dabei erzielt wurde die Digitalisierung und Leistungssteigerung entlang der gesamten Prozesskette, von der Formherstellung bis zum unternehmensübergreifenden Datenaustausch. Bei der Werkzeugherstellung konnten durch den Einsatz von maschinellem Lernen Modellierungsverfahren zur Vorhersage von Bauteilqualitäten entwickelt werden. Diese ermöglichen eine Prozessoptimierung in Echtzeit. Aufbauend drauf wurden intelligente Werkzeugsysteme entwickelt, welche durch Nachrüstung bestehender Werkzeuge und Druckgussanlagen mit kostengünstiger Messtechnik entstanden sind. Diese Aufrüstung ermöglicht eine datengetriebene Prozessanalyse, welche zu einer verbesserten Überwachung und Steuerung des Produktionsprozesses führt.
Dadurch wurde ein weiterer Schritt in Richtung adaptiver Prozessführung im Druckguss erreicht. Mit Dashboards können die prädiktiven Qualitätsprognosen und Trends mit Handlungsempfehlung an den Maschinenbediener weitergegeben werden, welcher proaktiv den Prozess anpassen kann. Prozessübergeordnet werden datengetriebene Ansätze verwendet, um die Produktionsplanung und -steuerung zu optimieren und Durchlauf- und Bearbeitungszeiten erfolgreich besser vorherzusagen. Für die Ermöglichung eines unternehmensübergreifenden Datenaustausches wurden IT-Architekturen geschaffen, welche die Datensouveränität der Unternehmen schützen.
Das „Zukunftslabor Produktion“ hat somit einen wichtigen Beitrag zur Weiterentwicklung der industriellen Produktion geleistet und legt den Grundstein für zukünftige Forschungsprojekte im Bereich der digitalisierten und autonomen Produktion.
Das Konsortium des Zukunftslabors Produktion dankt dem niedersächsischen Ministerium für Wissenschaft und Kultur für die finanzielle Förderung des Forschungsprojektes. Weitere Informationen zu dem Projekt und weiteren Zukunftslaboren sind abrufbar unter: https://zdin.de/zukunftslabore/produktion