Meilenstein in der CFK-Fertigung: IFW fertigt topologieoptimierte Rumpfstruktur im AFP-Prozess
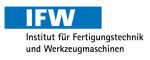

Das IFW hat einen etwa 1 x 1,5 m großen Demonstrator eines Flugzeugrumpfausschnitts gefertigt und damit einen durchgängigen Prozess zur Herstellung topologieoptimierter Faserverbundstrukturen validiert. Die gefertigte Struktur mit gitterversteifter Geometrie und schaumgefüllten Omega-Versteifungen demonstriert das Potenzial der Automated Fiber Placement (AFP) Technologie für innovative Leichtbaulösungen in der Luftfahrt.
Die Struktur dient als Konzeptnachweis für einen lastpfadgerechten Rumpfausschnitt des elektrisch angetriebenen Faserverbund-Flugzeuges MDA1 eViator, das im Projekt SHOREliner in einem Konsortium unter der Führung von MD Aircraft entwickelt wird.
Grundlage für die Umsetzung bildet ein multidisziplinärer Auslegungsprozess, der in Kooperation mit dem Institut für Flugzeugbau und Leichtbau (IFL) der TU Braunschweig entwickelt wurde. Bereits in der frühen Entwurfsphase wird die Struktur gezielt auf die Besonderheiten und Grenzen des AFP-Prozesses abgestimmt. Die vom IFL durchgeführte Topologieoptimierung bestimmt zunächst die optimale Anordnung der Versteifungselemente entsprechend der strukturellen Belastung. Darauf aufbauend erfolgt eine automatisierte Generierung der Versteifungsgeometrie unter Berücksichtigung der prozesstechnischen Randbedingungen der AFP-Technologie, eine Methodik, die im DFG-Projekt OptiFee erforscht und entwickelt wurde.
Durch die im Projekt OptiFee erarbeitete systematische Formalisierung des AFP-Fertigungswissens können fertigungsgerechte Geometrien automatisch anhand der technischen Parameter und Fähigkeiten des eingesetzten AFP-Systems erzeugt werden, ohne dass simulative oder experimentelle Fertigungsuntersuchungen als Zwischenschritte erforderlich sind. Dadurch konnte der gesamte Prozess vom Design bis zum fertigen Bauteil in weniger als fünf Wochen abgeschlossen werden.
Der Fertigungsprozess gliedert sich in mehrere Phasen: Nach Abschluss der Topologieoptimierung und Geometriegenerierung wird das CFK-Hautfeld zunächst im AFP-Prozess auf einem vorab eingemessenen Werkzeug abgelegt. Anschließend werden die CNC-gefrästen, luftfahrtzertifizierten Schaumkerne für die Omega-Versteifungen präzise positioniert und mithilfe epoxidbasierter Klebefilme fixiert. Zur Sicherstellung der erforderlichen Haftung während der weiteren Prozessschritte wird ein spezieller Sprühkleber auf die Oberflächen der Schaumkerne aufgebracht. Die CFK-Decklagen der Omega-Versteifungen werden danach ebenfalls im AFP-Prozess lokal auf die vorbereiteten Schaumkerne aufgebracht. Der abschließende Aushärtungsprozess des gesamten Bauteils erfolgt gemäß luftfahrtspezifischer Fertigungsstandards unter definierten Druck- und Temperaturbedingungen im Autoklav.
Das erfolgreich gefertigte Demonstratorbauteil validiert die neu entwickelte Methodik und unterstreicht das Potenzial für integrale, automatisiert gefertigte und gewichtsoptimierte Strukturlösungen in zukünftigen Luftfahrtanwendungen. Die in den Projekten gewonnenen Erkenntnisse schaffen eine belastbare Grundlage für die Weiterentwicklung ressourceneffizienter Herstellungsverfahren für komplexe CFK-Strukturen. Das Bauteil wurde vergangene Woche auf der Hannover Messe erstmals einem breiten Publikum präsentiert und ist diese Woche auf der AERO in Friedrichshafen zu besichtigen.
Das Projekt OptiFee wird durch die Deutsche Forschungsgemeinschaft (DFG) gefördert. Das IFW dankt der DFG für die finanzielle Unterstützung zur Durchführung des Projektes.
Das Projekt SHOREliner wird im Rahmen des sechsten zivilen Luftfahrtforschungsprogramms (LuFo VI-3) durch das Bundesministerium für Wirtschaft und Klimaschutz (BMWK) gefördert. Das IFW dankt dem BMWK für die finanzielle Unterstützung zur Durchführung des Projektes sowie den Partnern für die gute Zusammenarbeit.