Spannung komplexer Bauteile neu gedacht
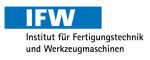

Mit additiven Fertigungsverfahren haben sich neue Gestaltungsmöglichkeiten für Bauteile eröffnet. Durch den schichtweisen Aufbau können Bauteile mit nahezu beliebiger Geometrie gefertigt werden. Bei der Konstruktion können Bauteile hierdurch für ihren Einsatzzweck optimal entworfen werden. Besondere Verbreitung finden additive Fertigungsverfahren daher bei der Herstellung von Leichtbaustrukturen.
Eine Herausforderung additiver Herstellungsverfahren ist die Fertigung von Funktionsflächen sowie die Einhaltung präziser Form- und Lagetoleranzen. Für die Fertigung präziser Endkonturen werden additiv hergestellte Bauteile daher spanend nachbearbeitet. Zur Bearbeitung müssen die Bauteile in der Bearbeitungsmaschine mittels geeigneter Spannmittel sicher eingespannt werden. Gängige Spannmittel wie z. B. Spannpratzen oder Schraubstöcke können oftmals nicht eingesetzt werden. Der Grund hierfür ist, dass durch die hohe geometrische Komplexität der Bauteile in der Regel keine geeigneten planaren oder zylindrische Spannflächen verfügbar sind. Zum Spannen des Werkstücks werden daher oftmals sogenannte Formspannbacken eingesetzt. Diese Spannbacken bilden an der Spannfläche eine Negativform des zu bearbeitenden Werkstücks ab und müssen individuell für das jeweilige Werkstück angefertigt werden.
Die Herstellung der Formspannbacken stellt somit einen zusätzlichen, nicht wertschöpfenden Fertigungsschritt dar. Zudem sind die Formspannbacken oftmals nur für ein spezifisches Werkstück anwendbar und können für weitere Werkstücke nicht wiederverwendet werden. Darüber hinaus werden in der Regel mehrere Aufspannungen benötigt, um sämtliche Funktionsflächen zu bearbeiten. Für eine weitere Aufspannung ist oftmals eine separate Spannvorrichtung erforderlich. Zudem sind mit einer weiteren Aufspannung oftmals zeitintensive Einmessvorgänge des Werkstücks verbunden, um die Lage und Orientierung des Werkstücks im Arbeitsraum der Werkzeugmaschine präzise zu bestimmen und somit auch enge Fertigungstoleranzen einzuhalten. Bei bestehenden Spannsystemen existiert darüber hinaus das Defizit, dass die Kontaktfläche des Werkstücks an den Spannfläche erst in einer weiteren Aufspannung bearbeitet werden kann. Ein Spannsystem, welches die Werkstückbearbeitung an sämtlichen Spann- und Funktionsflächen in nur einer Aufspannung ohne individuelle Spannbacken ermöglicht, bietet somit besonders hohes Potenzial, um Rüst- und Nebenzeiten deutlich zu mindern. Ein derartiges Spannsystem wird im nachfolgenden Abschnitt beschrieben.
Konzept ermöglicht Bearbeitung der Spannflächen ohne Umspannen
Im Bild ist das neuartige Spannkonzept für additiv gefertigte Bauteile schematisch dargestellt. Bei diesem Ansatz wird das Werkstück mithilfe von mehreren Spannmodulen fixiert. Jedes Spannmodul besteht dabei aus mehreren Stiften, die in einem Rastermuster angeordnet sind (Bildausschnitt a). Die Stifte sind dabei verschieblich gelagert und können in einer spezifischen Stellung arretiert werden. Im Verbund bilden die Stifte, analog zu bestehenden Formspannbacken, eine Negativform des zu spannenden Werkstücks ab. Derartige Spannmodule sind bereits am Markt verfügbar. Im Forschungsprojekt „AllSpann“ wird das Spannmodul mit einer unterlagerten Lineareinheit kombiniert. Dies erlaubt es, das Spannmodul jeweils in X-Richtung zu positionieren. Der Vorteil dieses Ansatzes wird in Bildausschnitt b) dargestellt. Durch einen Rückziehhub wird die Spannfläche bei einem Spannmodul für die Fräsbearbeitung zugänglich. Das Werkstück wird dabei durch die verbleibenden Spannmodule sicher fixiert. Nach der Bearbeitung an dieser Stelle, wird das Spannmodul erneut in Kontakt mit dem Werkstück gebracht und trägt somit zur sicheren Einspannung bei. Mit diesem Vorgehen können somit auch Spann- und Funktionsflächen bearbeitet werden, die bei konventionellen Spannvorrichtungen erst mit einer weiteren Aufspannung zugänglich sind. Damit entfallen auch zusätzliche Umspannvorgänge sowie die verbundenen Rüst- und Nebenzeiten.