DataPlan - Assistenzsystem zur datenbasierten Prüfplanung
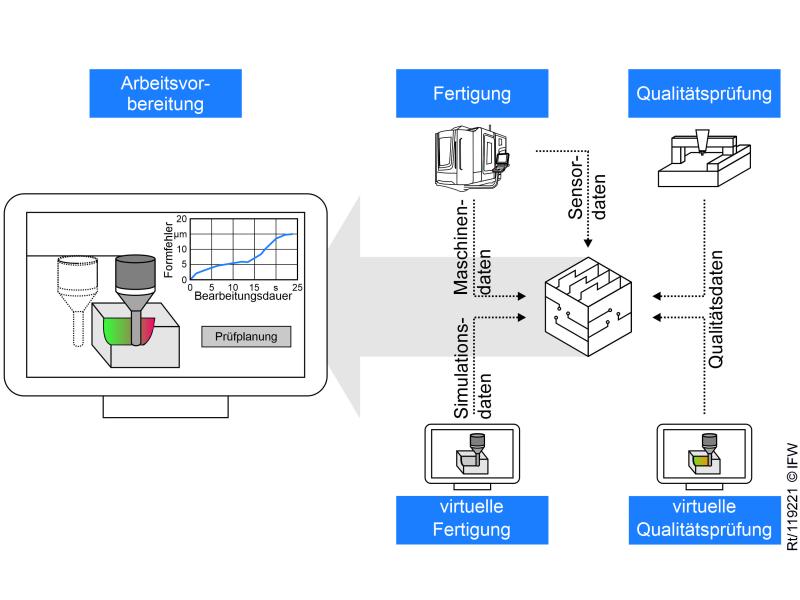
Das BMBF-geförderte KMU-innovativ-Verbundprojekt wird am Institut für Fertigungstechnik und Werkzeugmaschinen (IFW) in enger Zusammenarbeit mit den Unternehmen Brinkhaus GmbH und Toolcraft AG gestartet. Das Ziel des Projektes ist die Entwicklung eines Assistenzsystems zur datenbasierten Prüfplanung für eine additiv-subtraktive Prozesskette. Dazu werden die Qualitäts- und Fertigungsdaten synchronisiert und in die Arbeitsvorbereitung zurückgeführt. Dies ermöglicht eine datenbasierte Prognose der Werkstückqualität und somit reduzierte Aufwände innerhalb der Prüfplanung.
Die Prüfplanung hat sich in den letzten 30 Jahren nur unwesentlich weiterentwickelt. Derzeit findet im fertigungstechnischen Umfeld oftmals eine permanente Steuerung und Überwachung durch den Menschen statt. Somit wird in der Planung von Fertigungsprozessen auf das bestehende Erfahrungswissen des Mitarbeitenden zurückgegriffen, um die Relevanz eines Prüfmerkmals zu beurteilen. Ein vielversprechender Ansatz ist die Integration datenbasierter Ansätze in bestehende Produktionssysteme. Durch die steigende Digitalisierung des fertigungstechnischen Umfelds liegen immer mehr Daten vor, die bisher nicht ausreichend genutzt werden. Eine enorme Chance stellt die Künstliche Intelligenz (KI) dar, in dem große Datenmengen ausgewertet, aufbereitet sowie unterstützende Handlungsempfehlungen automatisch ausgesprochen werden. Durch die Integration datenbasierter Ansätze ist eine Prüfplanung auf Basis von Vergangenheitsdaten möglich. Dadurch sollen relevante Prüfmerkmale identifiziert und vermeidbare Prüfaufwände reduziert werden.
Die Grundvoraussetzung für die Entwicklung eines Assistenzsystems zur datenbasierten Prüfplanung besteht aus einer ausreichenden Datenverfügbarkeit. Derzeit erfordert das Auslesen von Daten aus der Maschinensteuerung einen hohen Aufwand und umfangreiches Know-How. Demzufolge wird in diesem Projekt eine nachhaltige Softwarelösung zum Auslesen von Maschinendaten erforscht. Während der Fertigung eines Bauteils fallen diverse Datenströme aus unterschiedlichen Datenquellen an, welche sich durch verschiedene Datenformate und -frequenzen unterscheiden. Diese sind maschineninterne Signale aus der Maschinensteuerung (Achsposition, Vorschubgeschwindigkeit, Schnittgeschwindigkeit, etc.), externe Signale aus Sensoren (Kraftsensoren, Wirkleistungssensoren, etc.) und Simulationsdaten einer Materialauftrags- bzw. abtragssimulation (Zeitspanvolumen, Werkzeugumschlingungswinkel, etc.). Hinzu kommen Daten aus vor- und nachgelagerten Prozessen. Eine Herausforderung besteht darin, diese Datenströme zu einer einheitlichen Datenbasis zu synchronisieren. Daher ist ein weiteres Teilziel die Entwicklung einer Methode zur Synchronisierung von unterschiedlichen Datenströmen, welche in die Arbeitsvorbereitung zurückgeführt werden. Anhand dessen können Abhängigkeiten zwischen den auftretenden Daten erkannt und für die Qualitätsprognose genutzt werden.
Die Erforschung des Assistenzsystems zur datenbasierten Prüfplanung wird an drei komplementären Anwendungsfällen (subtraktive, additiv-subtraktive und hybrid additive Bearbeitung) durchgeführt. Dadurch wird die Übertragbarkeit der Projektergebnisse untersucht und die prozessübergreifende Anwendung bewertet. Derzeit ist eine Visualisierung der zu erwartenden Werkstückqualität innerhalb gängiger CAM-Systeme nicht möglich. Aus diesem Grund sollen die entwickelten Prognosemodelle des maschinellen Lernens in die CAM-Software integriert werden. Die Rückführung von vergangenen Fertigungs- und Qualitätsdaten ermöglicht eine featureabhängige Modellierung der Werkstückqualität. Dadurch wird der Mitarbeitende bei der Auswahl passender Prozessstellgrößen sowie relevanter Prüfmerkmale im Rahmen einer datengetriebenen Handlungsempfehlung unterstützt. Die Entscheidung wird auf Basis eines standardisierten Vorgehens getroffen, wodurch die Abhängigkeit von Erfahrungswissen reduziert wird.
Kontakt:
Für weitere Informationen steht Ihnen Sarah Andrews, Institut für Fertigungstechnik und Werkzeugmaschinen der Leibniz Universität Hannover, unter Telefon +49 (0) 511 – 762 18320 oder per E-Mail (andrews@ifw.uni-hannover.de) gern zur Verfügung.
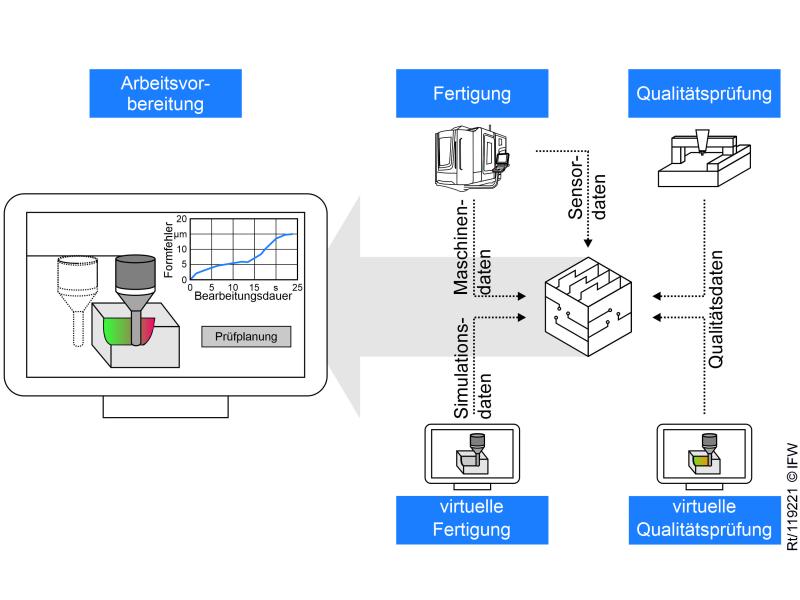
Das BMBF-geförderte KMU-innovativ-Verbundprojekt wird am Institut für Fertigungstechnik und Werkzeugmaschinen (IFW) in enger Zusammenarbeit mit den Unternehmen Brinkhaus GmbH und Toolcraft AG gestartet. Das Ziel des Projektes ist die Entwicklung eines Assistenzsystems zur datenbasierten Prüfplanung für eine additiv-subtraktive Prozesskette. Dazu werden die Qualitäts- und Fertigungsdaten synchronisiert und in die Arbeitsvorbereitung zurückgeführt. Dies ermöglicht eine datenbasierte Prognose der Werkstückqualität und somit reduzierte Aufwände innerhalb der Prüfplanung.
Die Prüfplanung hat sich in den letzten 30 Jahren nur unwesentlich weiterentwickelt. Derzeit findet im fertigungstechnischen Umfeld oftmals eine permanente Steuerung und Überwachung durch den Menschen statt. Somit wird in der Planung von Fertigungsprozessen auf das bestehende Erfahrungswissen des Mitarbeitenden zurückgegriffen, um die Relevanz eines Prüfmerkmals zu beurteilen. Ein vielversprechender Ansatz ist die Integration datenbasierter Ansätze in bestehende Produktionssysteme. Durch die steigende Digitalisierung des fertigungstechnischen Umfelds liegen immer mehr Daten vor, die bisher nicht ausreichend genutzt werden. Eine enorme Chance stellt die Künstliche Intelligenz (KI) dar, in dem große Datenmengen ausgewertet, aufbereitet sowie unterstützende Handlungsempfehlungen automatisch ausgesprochen werden. Durch die Integration datenbasierter Ansätze ist eine Prüfplanung auf Basis von Vergangenheitsdaten möglich. Dadurch sollen relevante Prüfmerkmale identifiziert und vermeidbare Prüfaufwände reduziert werden.
Die Grundvoraussetzung für die Entwicklung eines Assistenzsystems zur datenbasierten Prüfplanung besteht aus einer ausreichenden Datenverfügbarkeit. Derzeit erfordert das Auslesen von Daten aus der Maschinensteuerung einen hohen Aufwand und umfangreiches Know-How. Demzufolge wird in diesem Projekt eine nachhaltige Softwarelösung zum Auslesen von Maschinendaten erforscht. Während der Fertigung eines Bauteils fallen diverse Datenströme aus unterschiedlichen Datenquellen an, welche sich durch verschiedene Datenformate und -frequenzen unterscheiden. Diese sind maschineninterne Signale aus der Maschinensteuerung (Achsposition, Vorschubgeschwindigkeit, Schnittgeschwindigkeit, etc.), externe Signale aus Sensoren (Kraftsensoren, Wirkleistungssensoren, etc.) und Simulationsdaten einer Materialauftrags- bzw. abtragssimulation (Zeitspanvolumen, Werkzeugumschlingungswinkel, etc.). Hinzu kommen Daten aus vor- und nachgelagerten Prozessen. Eine Herausforderung besteht darin, diese Datenströme zu einer einheitlichen Datenbasis zu synchronisieren. Daher ist ein weiteres Teilziel die Entwicklung einer Methode zur Synchronisierung von unterschiedlichen Datenströmen, welche in die Arbeitsvorbereitung zurückgeführt werden. Anhand dessen können Abhängigkeiten zwischen den auftretenden Daten erkannt und für die Qualitätsprognose genutzt werden.
Die Erforschung des Assistenzsystems zur datenbasierten Prüfplanung wird an drei komplementären Anwendungsfällen (subtraktive, additiv-subtraktive und hybrid additive Bearbeitung) durchgeführt. Dadurch wird die Übertragbarkeit der Projektergebnisse untersucht und die prozessübergreifende Anwendung bewertet. Derzeit ist eine Visualisierung der zu erwartenden Werkstückqualität innerhalb gängiger CAM-Systeme nicht möglich. Aus diesem Grund sollen die entwickelten Prognosemodelle des maschinellen Lernens in die CAM-Software integriert werden. Die Rückführung von vergangenen Fertigungs- und Qualitätsdaten ermöglicht eine featureabhängige Modellierung der Werkstückqualität. Dadurch wird der Mitarbeitende bei der Auswahl passender Prozessstellgrößen sowie relevanter Prüfmerkmale im Rahmen einer datengetriebenen Handlungsempfehlung unterstützt. Die Entscheidung wird auf Basis eines standardisierten Vorgehens getroffen, wodurch die Abhängigkeit von Erfahrungswissen reduziert wird.
Kontakt:
Für weitere Informationen steht Ihnen Sarah Andrews, Institut für Fertigungstechnik und Werkzeugmaschinen der Leibniz Universität Hannover, unter Telefon +49 (0) 511 – 762 18320 oder per E-Mail (andrews@ifw.uni-hannover.de) gern zur Verfügung.