Intelligente Maschine: Prozessplanung selbstgemacht
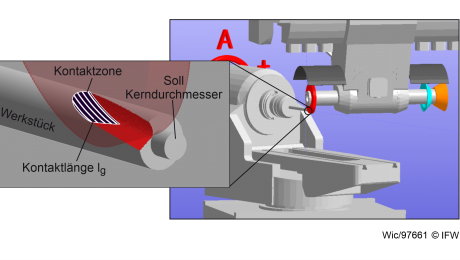
Die Prozessplanung und die optimale Einstellung der Prozessparameter sind vor allem für hochdynamische Anwendungen wie das Werkzeugschleifen sehr zeit- und kostenintensiv. Oftmals sind erfahrene Mitarbeiter erforderlich, die eine Vielzahl von Praxisversuchen durchführen müssen. Die Einstellung der Prozessparameter stark von der Erfahrung der Mitarbeiter abhängig und führt nicht immer zu einem optimal eingestellten Fertigungsprozess. Außerdem ist für jedes neue Material, für jede neue Schleifscheibe und für jede neue Prozessgeschwindigkeit eine erneute Einstellung der Parameter erforderlich. Wulf: „Trotz der aufwändigen Prozedur möchten die Kunden oftmals nur kleine Losgrößen zu möglichst geringen Preisen abnehmen. Das erhöht den Druck auf die Produzenten enorm und erfordert neue Lösungen.“
Das Projekt überwindet diese Herausforderung und stellt die Prozessplanung neu auf. Dabei ist eine Datenbank mit unterschiedlichen Prozessparametern und den resultierenden Werkstückendaten die Grundlage. Neue Datensätze kommen laufend in Form von gemessenen Werkstückeigenschaften und den zugehörigen Fertigungsparametern hinzu. Als Werkstückeigenschaften stehen vor allem die Formhaltigkeit, die Oberflächenqualität und die Eigenschaften der Randzone im Fokus.
Mit den gesammelten Datensätzen erstellen automatisierte Methoden des maschinellen Lernens Prognosemodelle, um die Werkstückeigenschaften unbekannter Prozesse vorauszusagen. Die Prognosegüte verbessert sich ständig, da die Datenbank immer weiterwächst. Dadurch kann die Maschine die Parameter schon vor der Fertigung optimieren und es sind keine Versuche mehr vor dem eigentlichen Start der Produktion erforderlich. Zudem benötigen die Mitarbeiter weniger Prozesswissen, was Urlaubsvertretungen oder den Ersatz eines kranken Mitarbeiters deutlich vereinfacht.
„Wir erreichen eine selbstoptimierende Werkzeugmaschine, die eigenständig Entscheidungen auf analytischen und empirischen Grundlagen trifft. Das minimiert die erforderlichen Ressourcen zur Prozessplanung und steigert so die Wettbewerbsfähigkeit der Werkzeugproduzenten. Die Entlastung der Maschinenbediener trägt außerdem zu einer angenehmeren Arbeitsatmosphäre bei“, fasst Wulf das Ziel des Projektes zusammen. Abschließend enthält das Projekt noch die Entwicklung einer allgemeinen Methodik, die das Prinzip der selbstoptimierenden Maschine auch auf andere Maschinentypen und weitere Prozesse überträgt.
Für weitere Informationen steht Ihnen Michael Wulf, Institut für Fertigungstechnik und Werkzeugmaschinen, unter der Telefonnummer +49 511 762 18354 oder per E-Mail unter wulf_m@ifw.uni-hannover.de gern zur Verfügung.
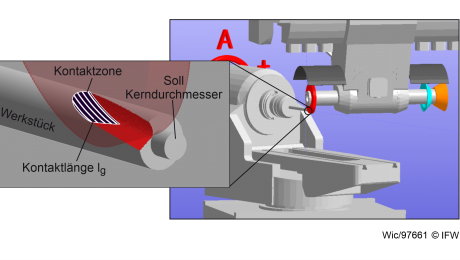
Die Prozessplanung und die optimale Einstellung der Prozessparameter sind vor allem für hochdynamische Anwendungen wie das Werkzeugschleifen sehr zeit- und kostenintensiv. Oftmals sind erfahrene Mitarbeiter erforderlich, die eine Vielzahl von Praxisversuchen durchführen müssen. Die Einstellung der Prozessparameter stark von der Erfahrung der Mitarbeiter abhängig und führt nicht immer zu einem optimal eingestellten Fertigungsprozess. Außerdem ist für jedes neue Material, für jede neue Schleifscheibe und für jede neue Prozessgeschwindigkeit eine erneute Einstellung der Parameter erforderlich. Wulf: „Trotz der aufwändigen Prozedur möchten die Kunden oftmals nur kleine Losgrößen zu möglichst geringen Preisen abnehmen. Das erhöht den Druck auf die Produzenten enorm und erfordert neue Lösungen.“
Das Projekt überwindet diese Herausforderung und stellt die Prozessplanung neu auf. Dabei ist eine Datenbank mit unterschiedlichen Prozessparametern und den resultierenden Werkstückendaten die Grundlage. Neue Datensätze kommen laufend in Form von gemessenen Werkstückeigenschaften und den zugehörigen Fertigungsparametern hinzu. Als Werkstückeigenschaften stehen vor allem die Formhaltigkeit, die Oberflächenqualität und die Eigenschaften der Randzone im Fokus.
Mit den gesammelten Datensätzen erstellen automatisierte Methoden des maschinellen Lernens Prognosemodelle, um die Werkstückeigenschaften unbekannter Prozesse vorauszusagen. Die Prognosegüte verbessert sich ständig, da die Datenbank immer weiterwächst. Dadurch kann die Maschine die Parameter schon vor der Fertigung optimieren und es sind keine Versuche mehr vor dem eigentlichen Start der Produktion erforderlich. Zudem benötigen die Mitarbeiter weniger Prozesswissen, was Urlaubsvertretungen oder den Ersatz eines kranken Mitarbeiters deutlich vereinfacht.
„Wir erreichen eine selbstoptimierende Werkzeugmaschine, die eigenständig Entscheidungen auf analytischen und empirischen Grundlagen trifft. Das minimiert die erforderlichen Ressourcen zur Prozessplanung und steigert so die Wettbewerbsfähigkeit der Werkzeugproduzenten. Die Entlastung der Maschinenbediener trägt außerdem zu einer angenehmeren Arbeitsatmosphäre bei“, fasst Wulf das Ziel des Projektes zusammen. Abschließend enthält das Projekt noch die Entwicklung einer allgemeinen Methodik, die das Prinzip der selbstoptimierenden Maschine auch auf andere Maschinentypen und weitere Prozesse überträgt.
Für weitere Informationen steht Ihnen Michael Wulf, Institut für Fertigungstechnik und Werkzeugmaschinen, unter der Telefonnummer +49 511 762 18354 oder per E-Mail unter wulf_m@ifw.uni-hannover.de gern zur Verfügung.
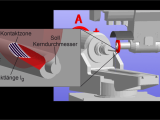