Optimierte Prognose der Bearbeitungsdauer durch Maschinenrückmeldedaten in Grey-Box-Modellen
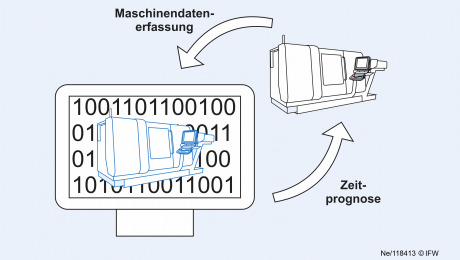
Für einen reibungslosen Ablauf in der Fertigung sind genaue Planzeiten der einzelnen Arbeitsgänge nötig. In der Praxis sind nach der Bearbeitung von Aufträgen Abweichungen zwischen den geplanten und realisierten Bearbeitungszeiten festzustellen. Dies trifft selbst auf Arbeitsgänge zu, die vollständig in CNC-Maschinen durchgeführt werden. Zurückzuführen sind die Bearbeitungszeitabweichungen auf ungenaue Simulationsmodelle für die NC-Codeausführung und Eingriffe von Maschinenbedienern, welche beispielsweise den Vorschub manuell angepasst haben. Besonders relevant sind in diesem Kontext Arbeitsgänge mit langer Bearbeitungsdauer und Arbeitsgangfolgen im mannlosen Betrieb, da diese bei Planungsabweichungen stärker ins Gewicht fallen. Arbeitsgänge mit langer Bearbeitungsdauer sind beispielsweise bei großen Bauteilen oder komplexen NC-Pfaden anzutreffen. Arbeitsgangfolgen im mannlosen Betrieb können mithilfe von Automatisierungssystemen, wie z.B. Werkstückspeichern, die einen mehrtägigen temporären autonomen Betrieb ermöglichen, umgesetzt werden.
Bisher können in NC-Code-Simulationen bereits Modelle konkreter Maschinen genutzt werden, um die Bearbeitungsdauer eines NC-Codes vor dem realen Prozess zu simulieren. Damit die Erstellung der Maschinenmodelle wirtschaftlich bleibt, ist die Modellierung der Maschinen- und Regelungseigenschaften nur in begrenztem Umfang möglich, woraus die genannten Abweichungen entstehen. Ein weiteres Problem ist der begrenzte Zugriff von Mitarbeitern in der Fertigungsplanung von kleinen und mittleren Unternehmen (KMU) auf kostenintensive Simulationsprogramme.
Abhilfe schaffen soll eine neue Methode, welche die präzise Prognose der Bearbeitungsdauer von NC-Codes durch den Einsatz eines maschinenspezifischen, datenbasierten digitalen Zwillings der CNC-Maschine ermöglicht. Dieser soll die Bearbeitungszeit von neuen NC-Programmen auf Basis von Rückmeldezeiten der Maschine bei der Bearbeitung vergangener NC-Codes prognostizieren. Durch die Nutzung von Methoden des maschinellen Lernens und den bidirektionalen Informationsfluss kann eine sich selbstoptimierende Prognosemethode entwickelt werden. Um die Datenmenge zum Anlernen zu reduzieren und auch bei geringen Datenmengen bereits industriell verwertbare Prognosen zu erhalten, sind Grey-Box-Modelle geeignet, welche die Vorteile von deterministischen Modellen (White-Box) und von datengetriebenen Ansätzen (Black-Box) miteinander vereinen. Das deterministische Modell soll für die Übertragbarkeit der zu entwickelnden Methode maschinenunabhängig sein und vereinfachte physikalische Formeln der Wirkzusammenhänge beinhalten, was zu Ungenauigkeiten der Prognosen führt. Kompensiert werden diese durch das datengetriebene Modell, welche das maschinenspezifische Verhalten abbilden und mit ansteigender Datenmenge eine verbesserte Prognosegüte liefern. Aufgenommen werden die Rückmeldezeiten prozessparallel durch eine Maschinendatenerfassung (MDE), ohne in den Bearbeitungsprozess einzugreifen.
Ziel des Zukunftslabors Produktion ist es, die Potenziale von durchgängig digitalen Prozessketten in der industriellen Produktion aufzuzeigen. Im Fokus stehen die Vernetzung, Modellierung und selbstständige Optimierung von Fertigungsverfahren, Prozessketten und Produktionsabläufen. Um die Produktion in Zukunft flexibler, intelligenter und ökologischer zu gestalten, werden maschinen- und prozessbezogene digitale Zwillinge eingesetzt.
Kontakt:
Für weitere Informationen steht Ihnen M. Eng. Marcus Nein, Institut für Fertigungstechnik und Werkzeugmaschinen der Leibniz Universität Hannover, unter Telefon +49 (0) 511 – 762 4365 oder per E-Mail nein@ifw.uni-hannover.de gern zur Verfügung.
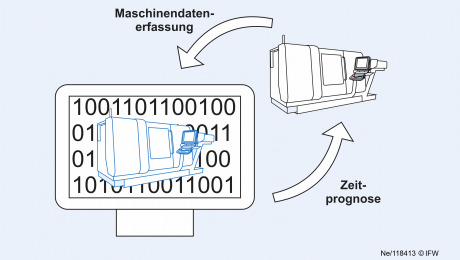
Für einen reibungslosen Ablauf in der Fertigung sind genaue Planzeiten der einzelnen Arbeitsgänge nötig. In der Praxis sind nach der Bearbeitung von Aufträgen Abweichungen zwischen den geplanten und realisierten Bearbeitungszeiten festzustellen. Dies trifft selbst auf Arbeitsgänge zu, die vollständig in CNC-Maschinen durchgeführt werden. Zurückzuführen sind die Bearbeitungszeitabweichungen auf ungenaue Simulationsmodelle für die NC-Codeausführung und Eingriffe von Maschinenbedienern, welche beispielsweise den Vorschub manuell angepasst haben. Besonders relevant sind in diesem Kontext Arbeitsgänge mit langer Bearbeitungsdauer und Arbeitsgangfolgen im mannlosen Betrieb, da diese bei Planungsabweichungen stärker ins Gewicht fallen. Arbeitsgänge mit langer Bearbeitungsdauer sind beispielsweise bei großen Bauteilen oder komplexen NC-Pfaden anzutreffen. Arbeitsgangfolgen im mannlosen Betrieb können mithilfe von Automatisierungssystemen, wie z.B. Werkstückspeichern, die einen mehrtägigen temporären autonomen Betrieb ermöglichen, umgesetzt werden.
Bisher können in NC-Code-Simulationen bereits Modelle konkreter Maschinen genutzt werden, um die Bearbeitungsdauer eines NC-Codes vor dem realen Prozess zu simulieren. Damit die Erstellung der Maschinenmodelle wirtschaftlich bleibt, ist die Modellierung der Maschinen- und Regelungseigenschaften nur in begrenztem Umfang möglich, woraus die genannten Abweichungen entstehen. Ein weiteres Problem ist der begrenzte Zugriff von Mitarbeitern in der Fertigungsplanung von kleinen und mittleren Unternehmen (KMU) auf kostenintensive Simulationsprogramme.
Abhilfe schaffen soll eine neue Methode, welche die präzise Prognose der Bearbeitungsdauer von NC-Codes durch den Einsatz eines maschinenspezifischen, datenbasierten digitalen Zwillings der CNC-Maschine ermöglicht. Dieser soll die Bearbeitungszeit von neuen NC-Programmen auf Basis von Rückmeldezeiten der Maschine bei der Bearbeitung vergangener NC-Codes prognostizieren. Durch die Nutzung von Methoden des maschinellen Lernens und den bidirektionalen Informationsfluss kann eine sich selbstoptimierende Prognosemethode entwickelt werden. Um die Datenmenge zum Anlernen zu reduzieren und auch bei geringen Datenmengen bereits industriell verwertbare Prognosen zu erhalten, sind Grey-Box-Modelle geeignet, welche die Vorteile von deterministischen Modellen (White-Box) und von datengetriebenen Ansätzen (Black-Box) miteinander vereinen. Das deterministische Modell soll für die Übertragbarkeit der zu entwickelnden Methode maschinenunabhängig sein und vereinfachte physikalische Formeln der Wirkzusammenhänge beinhalten, was zu Ungenauigkeiten der Prognosen führt. Kompensiert werden diese durch das datengetriebene Modell, welche das maschinenspezifische Verhalten abbilden und mit ansteigender Datenmenge eine verbesserte Prognosegüte liefern. Aufgenommen werden die Rückmeldezeiten prozessparallel durch eine Maschinendatenerfassung (MDE), ohne in den Bearbeitungsprozess einzugreifen.
Ziel des Zukunftslabors Produktion ist es, die Potenziale von durchgängig digitalen Prozessketten in der industriellen Produktion aufzuzeigen. Im Fokus stehen die Vernetzung, Modellierung und selbstständige Optimierung von Fertigungsverfahren, Prozessketten und Produktionsabläufen. Um die Produktion in Zukunft flexibler, intelligenter und ökologischer zu gestalten, werden maschinen- und prozessbezogene digitale Zwillinge eingesetzt.
Kontakt:
Für weitere Informationen steht Ihnen M. Eng. Marcus Nein, Institut für Fertigungstechnik und Werkzeugmaschinen der Leibniz Universität Hannover, unter Telefon +49 (0) 511 – 762 4365 oder per E-Mail nein@ifw.uni-hannover.de gern zur Verfügung.
