Vorspannungsdiagnose wie beim Arzt
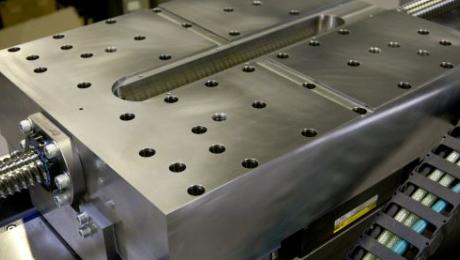
Den Wissenschaftlern vom Institut für Fertigungstechnik und Werkzeugmaschinen (IFW) der Leibniz Universität Hannover ist es gelungen, auf Basis einer multivariaten Auswertung von steuerungsinternen Informationen die Vorspannung von Kugelgewindetrieben für Werkzeugmaschinen zu klassifizieren.
Werkzeugmaschinen sind in der produzierenden Industrie weltweit nicht weg zu denken. Sie bilden zuverlässig das Rückgrat jeder Fertigung. Ein plötzlicher und somit ungeplanter Ausfall der Werkzeugmaschine führt je nach Auslastung der Fertigung zu hohen Folgekosten und nicht planbaren Abläufen in der Fertigungsplanung.
Laut Studien ist die Vorschubsachse mit Kugelgewindetrieben, trotz des sehr guten Wirkungsgrads, häufig Ursache für Ausfälle mit langen Stillstandzeiten. Detaillierte Untersuchungen haben ergeben, dass die Achsen zu hohen Teilen verschleißbedingt ausfallen. Die genaue Betrachtung des Kugelgewindetriebs ergibt, dass diese zur Sicherstellung einer hohen Achsdynamik bei gleichzeitiger hohen Positioniergenauigkeit vorgespannt sind.
Durch den stetigen Betrieb der Werkzeugmaschine und dem Verfahren der Achsen wird die Vorspannung langsam aber kontinuierlich verringert. Mit zunehmender Laufstrecke der Achsen sinkt die maximale Achsdynamik und Positioniergenauigkeit. Nach Unterschreitung eines anwendungsspezifischen Grenzwerts werden geforderte Eigenschaften nicht eingehalten und die Achse wird als Totalausfall charakterisiert. Ohne frühzeitige Vorhersage eines drohenden Achsausfalls ist ein schnelles und effizientes Eingreifen nicht möglich.
Gerade für in Zeiten von Just-In-Time Konzepten entsteht hierbei ein potentiell erheblicher wirtschaftlicher Schaden. Benötigte Ersatzkomponenten sind zumeist nicht lagernd verfügbar. Dies macht eine zustandsorientierte Instandhaltung umso wichtiger. Jedoch wird hierfür eine qualifizierte Aussage über den aktuellen Zustand des Kugelgewindetriebs benötigt. Für Kugelgewindetriebe mit Einzelmutter ist die Vorspannung im eingebauten Zustand in der Werkzeugmaschine nicht messbar. Häufig werden kostentreibende Sensoren wie bspw. Beschleunigungssensoren eingesetzt. Neben den hohen Anschaffungskosten entstehen weitere Kosten durch zusätzliche Montageaufwände. Trotz der höheren Aufwände ist die Lösung mit zusätzlichen Sensoren störanfälliger als Ansätze mit Steuerungsinformationen, die in jeder Werkzeugmaschine verfügbaren sind. Zu diesen zählen beispielsweise die Achs-Positionen oder die Drehmomente der Antriebe.
Deswegen hat das IFW in den vergangenen Monaten erfolgreich an Ansätzen geforscht die Vorspannung von Kugelgewindetrieben mit Einzelmuttern zu überwachen. Auf Basis der steuerungsinternen Informationen werden vorspannungssensitive Informationen extrahiert und zur Robustheits- und Sensitivitätssteigerung multivariat ausgewertet. Als Ergebnis lässt sich die Vorspannung der Kugelgewindetriebmutter durch einen Prüfzyklus klassifizieren. Beim Erreichen einer Warnschwelle können benötigte Ersatzteile rechtzeitig von der Instandhaltung bestellt werden. Somit ist eine schnelle Reaktion bei Ausfall der Komponenten gewährleistet oder der Ausfall wird im Vorhinein durch eine geplante zustandsorientierte Instandhaltung vermieden. Gleichzeitig werden Folgenkosten durch einen ungeplanten Stillstand der Komponente oder durch einen frühzeitigen Tausch der Komponente unterbunden.
Kontakt:
Für weitere Informationen steht Ihnen M. Sc. Alexander Schmidt, Institut für Fertigungstechnik und Werkzeugmaschinen, unter Telefon +49 511 762 18309 oder per E-Mail unter schmidt@ifw.uni-hannover.de gern zur Verfügung.
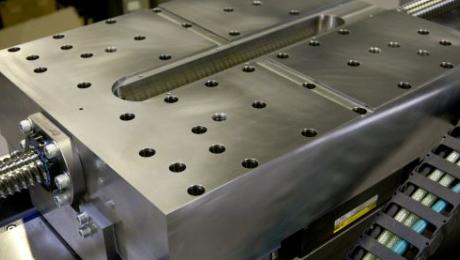
Den Wissenschaftlern vom Institut für Fertigungstechnik und Werkzeugmaschinen (IFW) der Leibniz Universität Hannover ist es gelungen, auf Basis einer multivariaten Auswertung von steuerungsinternen Informationen die Vorspannung von Kugelgewindetrieben für Werkzeugmaschinen zu klassifizieren.
Werkzeugmaschinen sind in der produzierenden Industrie weltweit nicht weg zu denken. Sie bilden zuverlässig das Rückgrat jeder Fertigung. Ein plötzlicher und somit ungeplanter Ausfall der Werkzeugmaschine führt je nach Auslastung der Fertigung zu hohen Folgekosten und nicht planbaren Abläufen in der Fertigungsplanung.
Laut Studien ist die Vorschubsachse mit Kugelgewindetrieben, trotz des sehr guten Wirkungsgrads, häufig Ursache für Ausfälle mit langen Stillstandzeiten. Detaillierte Untersuchungen haben ergeben, dass die Achsen zu hohen Teilen verschleißbedingt ausfallen. Die genaue Betrachtung des Kugelgewindetriebs ergibt, dass diese zur Sicherstellung einer hohen Achsdynamik bei gleichzeitiger hohen Positioniergenauigkeit vorgespannt sind.
Durch den stetigen Betrieb der Werkzeugmaschine und dem Verfahren der Achsen wird die Vorspannung langsam aber kontinuierlich verringert. Mit zunehmender Laufstrecke der Achsen sinkt die maximale Achsdynamik und Positioniergenauigkeit. Nach Unterschreitung eines anwendungsspezifischen Grenzwerts werden geforderte Eigenschaften nicht eingehalten und die Achse wird als Totalausfall charakterisiert. Ohne frühzeitige Vorhersage eines drohenden Achsausfalls ist ein schnelles und effizientes Eingreifen nicht möglich.
Gerade für in Zeiten von Just-In-Time Konzepten entsteht hierbei ein potentiell erheblicher wirtschaftlicher Schaden. Benötigte Ersatzkomponenten sind zumeist nicht lagernd verfügbar. Dies macht eine zustandsorientierte Instandhaltung umso wichtiger. Jedoch wird hierfür eine qualifizierte Aussage über den aktuellen Zustand des Kugelgewindetriebs benötigt. Für Kugelgewindetriebe mit Einzelmutter ist die Vorspannung im eingebauten Zustand in der Werkzeugmaschine nicht messbar. Häufig werden kostentreibende Sensoren wie bspw. Beschleunigungssensoren eingesetzt. Neben den hohen Anschaffungskosten entstehen weitere Kosten durch zusätzliche Montageaufwände. Trotz der höheren Aufwände ist die Lösung mit zusätzlichen Sensoren störanfälliger als Ansätze mit Steuerungsinformationen, die in jeder Werkzeugmaschine verfügbaren sind. Zu diesen zählen beispielsweise die Achs-Positionen oder die Drehmomente der Antriebe.
Deswegen hat das IFW in den vergangenen Monaten erfolgreich an Ansätzen geforscht die Vorspannung von Kugelgewindetrieben mit Einzelmuttern zu überwachen. Auf Basis der steuerungsinternen Informationen werden vorspannungssensitive Informationen extrahiert und zur Robustheits- und Sensitivitätssteigerung multivariat ausgewertet. Als Ergebnis lässt sich die Vorspannung der Kugelgewindetriebmutter durch einen Prüfzyklus klassifizieren. Beim Erreichen einer Warnschwelle können benötigte Ersatzteile rechtzeitig von der Instandhaltung bestellt werden. Somit ist eine schnelle Reaktion bei Ausfall der Komponenten gewährleistet oder der Ausfall wird im Vorhinein durch eine geplante zustandsorientierte Instandhaltung vermieden. Gleichzeitig werden Folgenkosten durch einen ungeplanten Stillstand der Komponente oder durch einen frühzeitigen Tausch der Komponente unterbunden.
Kontakt:
Für weitere Informationen steht Ihnen M. Sc. Alexander Schmidt, Institut für Fertigungstechnik und Werkzeugmaschinen, unter Telefon +49 511 762 18309 oder per E-Mail unter schmidt@ifw.uni-hannover.de gern zur Verfügung.
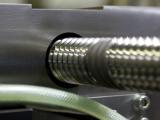
