Das Einmaleins des Werkzeug-Management - Stufe 2
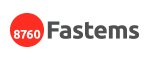
Stufe 2 - Kein Ausschuß und keine Spindekollisionen durch falsche Werkzeug-Offsets mehr
“T6345; 51.003 mm; 23.475 mm; 27.634 mm; 24.30 min”. – Eine Notiz auf dem Post-it erinnert den Maschinenbediener daran, welche Werkzeug-Offsets er in die Werkzeugmaschine einlegen muss.Zehnmal pro Tag ist der Maschinenbediener normalerweise damit beschäftigt. Nach jedem Einsatz muss jedes Schneidwerkzeug neu vermessen werden, und wenn ein Fehler gemacht wurde, können falsche Werkzeug-Offsets entweder Ausschussteile oder im schlimmsten Fall eine Spindelkollision verursachen.
Doch zum Glück passieren Fehler nur selten, oder?
Lassen Sie uns auch in diesem Post anhand eines Beipiels einfach mal durchrechnen, wie oft der Bediener eine lange Reihe vin Zahlen einzugeben hat und wie hoch dabei das Fehlerrisiko ist:
Ein Unternehmen fertigt auf 4 Werkzeugmaschinen:
Jede Maschine hat eine Laufzeit von 6.000 Stunden pro Jahr.
= 24.000 Bearbeitungsstunden pro Jahr
4 Werkzeugwechsel werden im Druchschnitt an jeder Werkzeugmaschine ausgeführt
= 96.000 Werkzeugwechsel pro Jahr
Es besteht ein Fehlerrisiko von 1 % (960 Fehler), von dem widerrum 1 % kritisch sind
und Spindelkollisionen verursachen
= 1 Spindelkollision
Wie hoch sind also die Kosten für 960 unbrauchbare Teile,
einschließlich deren Nachbearbeitungszeit?
Und was ist mit den durch die Spindelkollision verursachten Kosten?
Lesen Sie den vollständigen Blogpost und erfahren Sie mehr über den zweiten Schritt bei der Umsetzung der Best Practise im Werkzeug-Management und sparen Sie somit nicht nur wertvolle Zeit durch die Voreinstellung von Werkzeugen, sondern erfahren Sie auch wie Sie künftig Ausschuss und Spindelkollisionen vermeiden.